Matte glaze and preparation method thereof
A matte glaze and matte technology, applied in the field of ceramic decorative materials, can solve problems such as matte glaze roughness, reduce the melting temperature and widen the firing range.
- Summary
- Abstract
- Description
- Claims
- Application Information
AI Technical Summary
Problems solved by technology
Method used
Examples
Embodiment 1
[0070] In parts by weight, it includes: 4 parts of zinc oxide, 10 parts of barium carbonate, 5 parts of zirconium silicate, 15 parts of potassium feldspar, 20 parts of kaolin, 10 parts of calcite, 10 parts of burnt talcum powder, 28 parts of matte frit, Additive 1 part;
[0071] In parts by weight, the matte frit comprises: SiO 2 40 parts, Al 2 o 3 20 parts, Fe 2 o 3 0.5 parts, 5 parts of CaO, 1 part of MgO, K 2 O 1 part, Na 2 O 5 parts, ZnO 7 parts, B 2 o 3 0.5 parts, BaO 15 parts;
[0072] The additive is hydroxymethyl cellulose.
[0073] Preparation method of matte glaze:
[0074] Preparation of matte frit: mix quartz powder, potassium feldspar, raw zinc oxide, boric acid, limestone, dolomite, aluminum oxide, barium carbonate, and the above-mentioned component particles evenly, then use a pool furnace to melt the frit, and after firing The glass melt is fired at a temperature of 1400°C, and the frit particles are made into frit p...
Embodiment 2
[0081] In parts by weight, it includes: 4 parts of zinc oxide, 10 parts of barium carbonate, 5 parts of zirconium silicate, 15 parts of potassium feldspar, 20 parts of kaolin, 10 parts of calcite, 10 parts of burnt talcum powder, 28 parts of matte frit, Additive 1 part;
[0082] In parts by weight, the matte frit comprises: SiO 2 40 parts, Al 2 o 3 20 parts, Fe 2 o 3 0.5 parts, 5 parts of CaO, 1 part of MgO, K 2 O 1 part, Na 2 O 5 parts, ZnO 7 parts, B 2 o 3 0.5 parts, BaO 15 parts;
[0083] The additive is hydroxymethyl cellulose.
[0084] Preparation method of matte glaze:
[0085] Preparation of matte frit: mix quartz powder, potassium feldspar, raw zinc oxide, boric acid, limestone, dolomite, aluminum oxide, barium carbonate, and the above-mentioned component particles evenly, then use a pool furnace to melt the frit, and after firing The glass melt is fired at a temperature of 1400°C, and the frit particles are made into frit par...
PUM
Property | Measurement | Unit |
---|---|---|
time | aaaaa | aaaaa |
time | aaaaa | aaaaa |
hygroscopic ratio | aaaaa | aaaaa |
Abstract
Description
Claims
Application Information
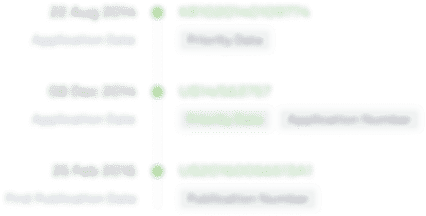
- R&D
- Intellectual Property
- Life Sciences
- Materials
- Tech Scout
- Unparalleled Data Quality
- Higher Quality Content
- 60% Fewer Hallucinations
Browse by: Latest US Patents, China's latest patents, Technical Efficacy Thesaurus, Application Domain, Technology Topic, Popular Technical Reports.
© 2025 PatSnap. All rights reserved.Legal|Privacy policy|Modern Slavery Act Transparency Statement|Sitemap|About US| Contact US: help@patsnap.com