Research on the high mechanical strength properties of HDPE (High-Density Polyethylene) - Eureka
HDPE Mechanical Strength Goals and Background
This research aims to delve into the underlying mechanisms and factors contributing to HDPE's remarkable mechanical strength. It will explore the molecular structure, crystallinity, and processing techniques that influence its mechanical properties. Additionally, the study will examine potential enhancements or modifications to further improve HDPE's mechanical performance, enabling the development of advanced materials for demanding applications across industries such as construction, automotive, and packaging.
Market Demand for High-Strength HDPE
- Growing Demand for High-Strength Materials
The market for high-strength materials like HDPE is expanding rapidly due to increasing demand from various industries such as construction, automotive, and packaging. These sectors require materials with superior mechanical properties to enhance product durability and safety. - Lightweight and Cost-Effective Solutions
HDPE offers a lightweight yet high-strength alternative to traditional materials like metals and composites. Its cost-effectiveness and ease of processing make it an attractive choice for manufacturers seeking to reduce production costs and improve efficiency. - Sustainability and Environmental Considerations
The recyclability and low carbon footprint of HDPE align with the growing emphasis on sustainability and environmental responsibility in various industries. This factor contributes to the increasing demand for HDPE-based products. - Infrastructure and Construction Applications
The construction industry is a significant consumer of high-strength HDPE materials. Applications include piping systems, geomembranes, and structural components, where HDPE's durability and resistance to corrosion and chemicals are highly valued. - Automotive and Transportation Sector
The automotive and transportation sectors are continuously seeking lightweight materials to improve fuel efficiency and reduce emissions. HDPE's high strength-to-weight ratio makes it an attractive choice for various automotive components and transportation infrastructure.
Current State and Challenges in HDPE Strength
- Current Challenges
Insufficient mechanical strength limits HDPE's applications in high-load environments. Enhancing strength without compromising other properties is a key challenge. - Geographical Distribution
Research on HDPE strength is globally distributed, with major contributions from the US, Europe, and Asia. However, a lack of standardization hinders collaboration. - Technical Bottlenecks
- Understanding the relationship between molecular structure and mechanical properties
- Developing effective reinforcement methods without introducing defects
- Balancing strength enhancement with other desirable properties like processability
Evolution of HDPE Strengthening Techniques
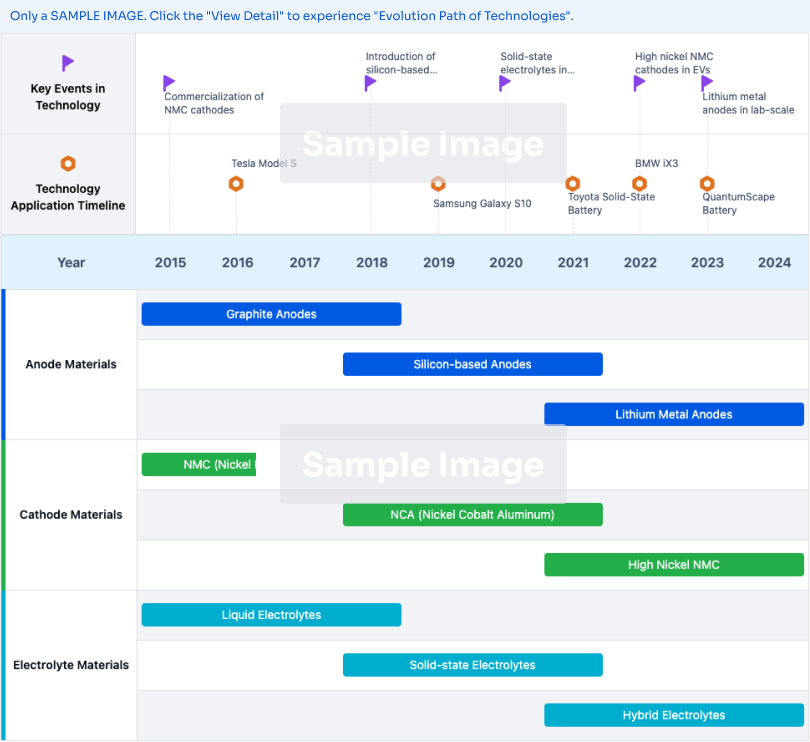
Existing Solutions for Enhancing HDPE Strength
01 HDPE Composites with Enhanced Mechanics
HDPE composites incorporating reinforcing fibers, nanoparticles, or additives have been developed to improve mechanical strength, impact resistance, and overall performance.- HDPE Monofilaments and Composites: HDPE can produce monofilaments and composites with enhanced mechanical properties like high strength, impact resistance, and durability for various applications.
- Reinforced HDPE Pipes: HDPE pipes can be reinforced with materials like steel wires, fibers, or ribs to increase mechanical strength and pressure resistance for applications requiring high structural integrity.
- Improved HDPE Properties: HDPE materials can be modified or combined with polymers or additives to enhance properties like heat resistance, electrical conductivity, antibacterial properties, and aging resistance for various industries.
- HDPE Alloys and Composites: HDPE can be alloyed or combined with other polymers like polyamides or ethylene-propylene copolymers to create new materials with tailored mechanical, thermal, and chemical resistance properties.
- HDPE Membranes and Films: HDPE can produce membrane and film structures with properties like high foaming, waterproofing, and wear resistance for applications in construction, packaging, and protective coatings.
02 High-Strength HDPE Pipes
HDPE pipes with enhanced strength and pressure resistance, reinforced with steel wires, ribs, or structural elements, have been developed for water supply, drainage, and gas transportation.03 High-Density HDPE with Improved Mechanics
Techniques have been developed to produce high-density HDPE materials with improved mechanical properties like high tensile strength, impact resistance, and wear resistance for applications requiring high mechanical performance.04 HDPE Alloys and Blends
HDPE can be alloyed or blended with other polymers or additives to create materials with improved mechanical properties like increased toughness, stiffness, or heat resistance, tailored for specific applications.05 HDPE Recycling and Processing
Techniques have been developed for recycling and processing HDPE to improve its mechanical properties, involving methods for regenerating HDPE particles, foaming, or other processes to enhance strength, toughness, or desired characteristics.
Key Players in HDPE Manufacturing
Borealis AG
Dow Global Technologies LLC
Core Innovations in HDPE Strengthening
- The ability to control the bimodality of the polymer by tuning the density, resulting in a multimodal hdpe resin with improved mechanical properties, specifically for use in caps and closures for bottles. the invention provides a single-site catalysed hdpe resin that has a density in the range of 952 to 970 kg/m3 and an mfr2 of 0.1 to 4.0 g/10 min. the resin comprises two fractions: a lower molecular weight fraction, which is an ethylene homopolymer or copolymer with a density in the range of 955 to 970 kg/m3 and an mfr2 of 10 to 400 g/10 min, and a higher molecular weight fraction, which is an ethylene homopolymer or copolymer with a density in the range of 940 to 960 kg/m3 and an mfr2 of 0.01 to 1.0 g/10 min. the process for preparing the multimodal hdpe involves polymerizing ethylene, optionally with comonomers, in three stages using a single site catalyst. the resulting ethylene polymer mixture is then further polymerized to obtain the multimodal hdpe resin. the composition of the invention includes the multimodal hdpe resin and a hydrocarbon resin. injection-molded articles, such as caps and closures for bottles, can be made from the multimodal hdpe resin or the composition.