Research on the good compatibility of HDPE (High-Density Polyethylene) - Eureka
SEP 30, 20244 MIN READ
Generate Your Technical Report in Patsnap Eureka
AI-Powered Innovation Solution Platform for R&D
HDPE Compatibility Challenges and Goals
The primary objective is to investigate the compatibility of high-density polyethylene (HDPE) with various materials and environments, aiming to enhance its versatility and broaden its application scope.
HDPE is a widely used thermoplastic polymer known for its exceptional strength, durability, and chemical resistance. However, its compatibility with certain materials and environments can be a limiting factor in specific applications. This research aims to explore strategies to improve HDPE's compatibility, such as through chemical modifications, blending with other polymers, or incorporating additives. The findings will contribute to expanding HDPE's potential uses in industries like packaging, construction, and automotive, where compatibility is crucial for performance and longevity.
HDPE is a widely used thermoplastic polymer known for its exceptional strength, durability, and chemical resistance. However, its compatibility with certain materials and environments can be a limiting factor in specific applications. This research aims to explore strategies to improve HDPE's compatibility, such as through chemical modifications, blending with other polymers, or incorporating additives. The findings will contribute to expanding HDPE's potential uses in industries like packaging, construction, and automotive, where compatibility is crucial for performance and longevity.
Market Demand for HDPE Applications
- Market Size and Growth
HDPE has a wide range of applications across various industries, including packaging, construction, automotive, and consumer goods. The global HDPE market is expected to grow steadily, driven by increasing demand from emerging economies and the shift towards sustainable materials. - Industry Trends
Key trends shaping the HDPE market include the rise of e-commerce and the need for lightweight, durable packaging materials, the growing demand for energy-efficient building materials, and the increasing adoption of HDPE in the automotive industry for weight reduction and fuel efficiency. - Application Sectors
- Packaging: HDPE is widely used for bottles, containers, and films due to its excellent moisture barrier properties and chemical resistance.
- Construction: HDPE pipes, geomembranes, and insulation materials are popular in the construction industry for their durability and cost-effectiveness.
- Automotive: HDPE is increasingly used in automotive applications, such as fuel tanks, interior trim, and exterior components, due to its lightweight and impact resistance.
- Regional Demand
Asia-Pacific region is expected to be the largest consumer of HDPE, driven by rapid industrialization and urbanization in countries like China and India. North America and Europe also have significant demand for HDPE, particularly in the packaging and construction sectors.
Current State and Limitations of HDPE Compatibility
- Compatibility Challenges HDPE exhibits limited compatibility with other materials, making it difficult to blend or combine with additives, fillers, or other polymers.
- Processing Limitations The high melt viscosity and crystalline nature of HDPE can lead to processing challenges, such as poor dispersion of additives and fillers, and difficulties in achieving desired mechanical properties.
- Environmental Stress Cracking HDPE is susceptible to environmental stress cracking, which can cause premature failure of products when exposed to certain chemicals or stress conditions.
- Thermal Stability Issues The thermal stability of HDPE can be a concern, particularly at high processing temperatures, leading to potential degradation and loss of mechanical properties.
Evolution of HDPE Technologies
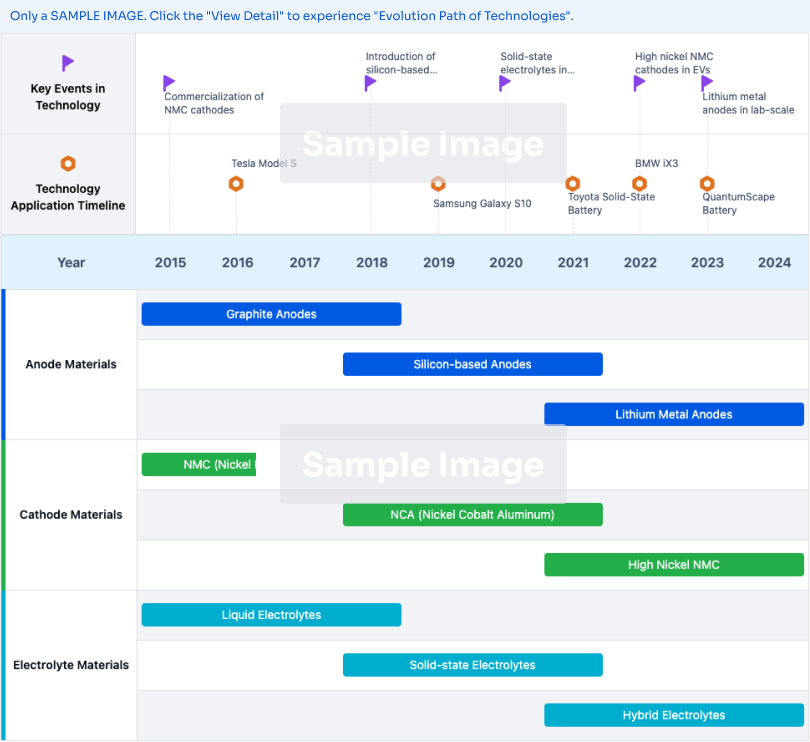
Existing Solutions for HDPE Compatibility
01 HDPE Composite Materials
Composite materials based on HDPE with reinforcements, fillers, or other polymers to enhance properties like strength, thermal resistance, conductivity, or compatibility.- HDPE Composite Materials: Composite materials incorporating additives or fillers into HDPE to improve properties like strength, conductivity, heat resistance, and flame retardancy for applications in construction, automotive, and electrical industries.
- HDPE Blends and Alloys: HDPE blended or alloyed with other polymers like PE, PP, or PVC to enhance compatibility, processability, and performance, exhibiting improved properties compared to individual components.
- HDPE Pipe and Fitting Materials: Specialized HDPE materials for pipes and fittings with improved pressure resistance, corrosion resistance, and wear resistance for water supply, gas transportation, and chemical handling applications.
- HDPE Film and Sheet Materials: HDPE processed into films and sheets with high strength, penetration resistance, and heat resistance for packaging, construction, and protective applications.
- Recycling and Modification of HDPE: Processes for recycling and modifying HDPE materials, such as reclaiming scrap or modifying properties through chemical or physical treatments, aiming to reduce waste and improve performance.
02 HDPE Pipe and Fitting Materials
Specialized HDPE materials for pipes and fittings with improved pressure resistance, corrosion resistance, and wear resistance for water supply, gas transportation, and chemical industries.03 HDPE Film and Sheet Materials
HDPE formulated into thin films and sheets with enhanced properties like high dielectric strength, insulation, penetration resistance, and aging resistance for packaging, electrical insulation, and protective barriers.04 HDPE Blends and Alloys
HDPE blended or alloyed with other polymers like PVC, PP, or LDPE to improve compatibility, processability, or introduce new properties for tailored performance.05 Recycling and Reuse of HDPE
Processes and methods for recycling and reusing HDPE materials, including industrial scrap and post-consumer waste, involving separation, cleaning, and reprocessing for new products or composite materials, promoting sustainability and resource efficiency.
Key Players in HDPE Industry
The research reveals a mature industry with significant market scale for HDPE (High-Density Polyethylene) compatibility. Key players like Borealis AG, Dow Global Technologies LLC, China Petroleum & Chemical Corp., ExxonMobil Chemical Patents, Inc., and SABIC Global Technologies BV have established themselves as leaders, demonstrating high technical maturity. The market is well-developed, with ongoing innovations aimed at enhancing HDPE compatibility for various applications, indicating a stable yet competitive environment.
Borealis AG
Technical Solution: Borealis AG has developed advanced HDPE grades with excellent compatibility using their Borstar technology, allowing for enhanced mechanical properties and processability.
Strength: Advanced Borstar technology. Weakness: Limited market penetration in some regions.
Dow Global Technologies LLC
Technical Solution: Dow Global Technologies LLC offers HDPE products with high compatibility through their proprietary INSITE technology, enabling precise control over polymer architecture for superior performance.
Strength: Proprietary INSITE technology. Weakness: Higher production costs.
Core Innovations in HDPE Compatibility
Blending virgin HDPE with post-consumer recycled HDPE and its method
PatentPendingJP2024523164A
Innovation
- Blending virgin HDPE with post-consumer recycled HDPE to improve processability and mechanical properties
- Composite manufacturing process for virgin and recycled HDPE blends
- Utilization of the blends in products and food packaging
Environmental Impact of HDPE
High-density polyethylene (HDPE) is a thermoplastic polymer widely used in various applications due to its excellent chemical resistance, durability, and cost-effectiveness. Ensuring good compatibility between HDPE and other materials or components is crucial for product performance and longevity. This research aims to explore techniques and strategies to enhance the compatibility of HDPE with different substances, surfaces, or environments. By understanding the factors influencing compatibility, such as surface properties, chemical interactions, and processing conditions, innovative solutions can be developed to improve adhesion, prevent delamination, and extend the service life of HDPE-based products. Ultimately, this research will contribute to the development of more reliable and efficient HDPE applications across various industries.
the structure of the environmentally friendly knitted fabric provided by the present invention; figure 2 Flow chart of the yarn wrapping machine for environmentally friendly knitted fabrics and storage devices; image 3 Is the parameter map of the yarn covering machine
Login to View More Regulatory Landscape for HDPE Applications
High-density polyethylene (HDPE) is a thermoplastic polymer widely used in various applications due to its excellent chemical resistance, durability, and cost-effectiveness. Ensuring good compatibility between HDPE and other materials or components is crucial for product performance and longevity. This research aims to explore techniques and strategies to enhance the compatibility of HDPE with different substances, surfaces, or environments. Key areas of focus include surface modification methods, compatibilizer additives, and processing conditions that can improve adhesion, wettability, and interfacial interactions. The findings will contribute to the development of high-performance HDPE-based products across industries such as packaging, construction, and automotive.
the structure of the environmentally friendly knitted fabric provided by the present invention; figure 2 Flow chart of the yarn wrapping machine for environmentally friendly knitted fabrics and storage devices; image 3 Is the parameter map of the yarn covering machine
Login to View More If you want an in-depth research or a technical report, you can always get what you want in Patsnap Eureka TechResearch . Try now!