Research on the properties and applications of nanocomposite high-density polyethylene (HDPE) - Eureka
OCT 8, 20243 MIN READ
Generate Your Technical Report in Patsnap Eureka
AI-Powered Innovation Solution Platform for R&D
Nanocomposite HDPE Properties and Goals
The primary objective is to provide a comprehensive overview of the development history, current status, and future trends of nanocomposite high-density polyethylene (HDPE) technology. This section will explore the key milestones and driving forces behind the evolution of this technology, shedding light on the motivations and goals that have shaped its progress over time.
Additionally, it will clearly define the expected technological targets and advancements that researchers and industry players aim to achieve in the field of nanocomposite HDPE. This will serve as a guiding framework for the subsequent analysis and discussions presented in the report, ensuring a focused and coherent exploration of this technology's potential applications and impact.
Additionally, it will clearly define the expected technological targets and advancements that researchers and industry players aim to achieve in the field of nanocomposite HDPE. This will serve as a guiding framework for the subsequent analysis and discussions presented in the report, ensuring a focused and coherent exploration of this technology's potential applications and impact.
Market Demand for Nanocomposite HDPE Applications
- Market Size and Growth
Nanocomposite HDPE has a wide range of applications in various industries, including automotive, construction, packaging, and consumer goods. The global market for nanocomposite HDPE is expected to grow significantly due to its superior properties and increasing demand for lightweight and high-performance materials. - Industry Trends
The automotive industry is a major driver for the adoption of nanocomposite HDPE, as it offers weight reduction and improved mechanical properties for vehicle components. The construction industry is also embracing nanocomposite HDPE for its durability and resistance to harsh environments. - Regional Demand
The Asia-Pacific region is projected to be the largest market for nanocomposite HDPE, driven by rapid industrialization and infrastructure development. North America and Europe are also significant markets due to stringent regulations and demand for sustainable materials. - Application Areas
Nanocomposite HDPE finds applications in automotive parts (bumpers, dashboards, interior trims), construction materials (pipes, geomembranes, roofing), packaging (bottles, containers), and consumer goods (sports equipment, household items).
Current State and Challenges of Nanocomposite HDPE
- Current Development Status Nanocomposite HDPE has gained significant attention due to its enhanced mechanical, thermal, and barrier properties compared to conventional HDPE. Researchers have explored various nanofillers, such as carbon nanotubes, graphene, and nanoclay, to improve the performance of HDPE.
- Key Challenges
- Achieving uniform dispersion of nanofillers in the HDPE matrix
- Ensuring strong interfacial adhesion between nanofillers and HDPE
- Maintaining processability and cost-effectiveness
- Geographical Distribution Research on nanocomposite HDPE is being conducted globally, with major contributions from the United States, Europe, and Asia, particularly China, Japan, and South Korea.
Evolution of Nanocomposite HDPE Technologies
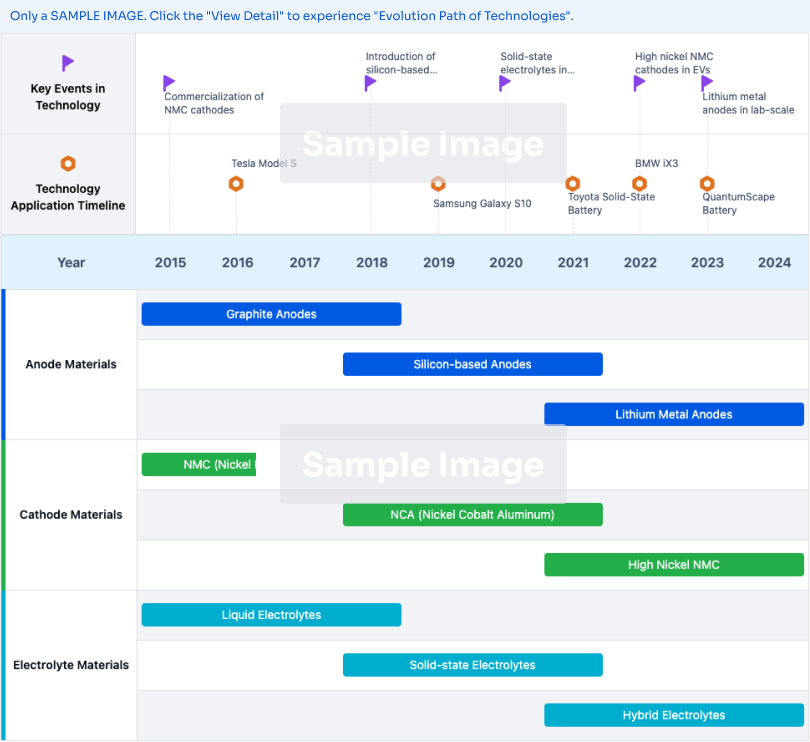
Existing Solutions for Nanocomposite HDPE
01 Organoclays or Nanoclays Incorporation
Incorporating organoclays or nanoclays into HDPE nanocomposites improves barrier, mechanical, and thermal properties. The nanoclays act as reinforcing agents, creating a tortuous path for gas molecules, enhancing barrier performance. They also increase stiffness, strength, and heat resistance.- Organoclays or Nanoclays Incorporation: Incorporating organoclays or nanoclays into HDPE nanocomposites enhances barrier, mechanical, and thermal properties. The nanoclays act as reinforcing agents, creating a tortuous path for gas molecules, improving barrier performance. They also increase stiffness and strength.
- Carbon Nanotubes or Graphene Utilization: Incorporating carbon nanotubes or graphene into HDPE nanocomposites improves mechanical, thermal, and barrier properties. These nanofillers act as reinforcing agents, enhancing strength, stiffness, and thermal conductivity. They also create a tortuous path for gas molecules, improving barrier performance.
- Nanoparticles or Nanofillers Incorporation: Incorporating nanoparticles or nanofillers like silica, alumina, or metal oxides into HDPE nanocomposites enhances mechanical, thermal, and barrier properties. These nanofillers act as reinforcing agents, increasing strength, stiffness, and thermal stability. They also create a tortuous path for gas molecules, improving barrier performance.
- Blending with Other Polymers or Elastomers: Blending HDPE with other polymers or elastomers forms nanocomposites with improved mechanical, thermal, and barrier properties. Adding nanofillers to these polymer blends further enhances the nanocomposite properties. Blending improves impact strength, flexibility, and barrier performance.
- Nucleating Agents or Compatibilizers Utilization: Incorporating nucleating agents or compatibilizers into HDPE nanocomposites improves nanofiller dispersion and enhances interfacial adhesion between HDPE matrix and nanofillers. This leads to improved mechanical, thermal, and barrier properties. Nucleating agents also improve crystallinity and barrier properties.
02 Carbon Nanotubes or Graphene Utilization
Incorporating carbon nanotubes or graphene into HDPE nanocomposites improves mechanical, thermal, and barrier properties. These nanofillers act as reinforcing agents, enhancing strength, stiffness, and heat resistance. They also create a tortuous path for gas molecules, improving barrier performance.03 Nanoparticles or Nanofillers Incorporation
Incorporating nanoparticles or nanofillers like silica, alumina, or metal oxides into HDPE nanocomposites improves mechanical, thermal, and barrier properties. These nanofillers act as reinforcing agents, enhancing strength, stiffness, and heat resistance. They also create a tortuous path for gas molecules, improving barrier performance.04 Nucleating Agents Incorporation
Incorporating nucleating agents into HDPE nanocomposites improves barrier and mechanical properties. Nucleating agents promote smaller and more uniform crystalline structures, creating a tortuous path for gas molecules, enhancing barrier performance. They also increase stiffness and strength.05 Multilayer or Nanocomposite Coatings Utilization
Using multilayer or nanocomposite coatings, like thermal barrier coatings or barrier films, improves thermal and barrier properties of HDPE-based materials. These coatings act as insulating layers, reducing heat transfer and improving thermal resistance. They also create a tortuous path for gas molecules, enhancing barrier performance.
Key Players in Nanocomposite HDPE Industry
The competitive landscape for nanocomposite high-density polyethylene (HDPE) is characterized by a mix of established companies and research institutions. The industry is in a growth phase with increasing market demand and expanding applications.
Borealis AG
Technical Solution: Borealis AG develops advanced nanocomposite HDPE materials with improved strength, durability, and thermal stability by integrating nanoparticles uniformly within the HDPE matrix.
Strength: High mechanical strength and thermal stability. Weakness: High production cost.
China Petroleum & Chemical Corp.
Technical Solution: China Petroleum & Chemical Corp. focuses on developing nanocomposite HDPE with enhanced barrier properties and environmental resistance using functionalized nanoparticles.
Strength: Enhanced barrier properties. Weakness: Complex manufacturing process.
Core Innovations in Nanocomposite HDPE
High-density polyethylene-graphene nanocomposites and methods thereof
PatentInactiveUS20170137596A1
Innovation
- The designing of polymer chain structure at a molecular level using metallocene catalysts, the incorporation of long chain branching to enhance mechanical strength, chemical resistance, flame retardency, and gas barrier properties, and the development of polyolefin nanocomposites to address shortcomings in conventional polyolefins. by incorporating nanofillers with specific dimensions in the polymer matrix, these nanocomposites aim to improve characteristics such as mechanical strength, chemical resistance, and gas barrier properties.
- The scheme discusses the potential applications of polyolefin nanocomposites in various industries, including packaging, automotive, and agriculture.
Environmental Impact of Nanocomposite HDPE
Nanocomposite high-density polyethylene (HDPE) is a promising material that combines the properties of HDPE and nanomaterials, offering enhanced mechanical, thermal, and barrier properties. The incorporation of nanofillers like carbon nanotubes, graphene, or clay nanoparticles into the HDPE matrix can significantly improve its performance. This technology has potential applications in various industries, including packaging, automotive, construction, and electronics, where lightweight, durable, and high-performance materials are desired. The report will explore the current state of research, key challenges, and future directions in developing and utilizing nanocomposite HDPE for advanced applications.
the structure of the environmentally friendly knitted fabric provided by the present invention; figure 2 Flow chart of the yarn wrapping machine for environmentally friendly knitted fabrics and storage devices; image 3 Is the parameter map of the yarn covering machine
Login to View More Regulatory Standards for Nanocomposite HDPE
Nanocomposite high-density polyethylene (HDPE) is a promising material that combines the properties of HDPE and nanomaterials, offering enhanced mechanical, thermal, and barrier properties. The incorporation of nanofillers like carbon nanotubes, graphene, or nanoclay into the HDPE matrix can significantly improve its performance. These nanocomposites have potential applications in various industries, including packaging, automotive, construction, and electronics, due to their superior strength, durability, and thermal stability. However, challenges such as uniform dispersion of nanofillers, interfacial compatibility, and cost-effective manufacturing processes need to be addressed for widespread commercial adoption.
the structure of the environmentally friendly knitted fabric provided by the present invention; figure 2 Flow chart of the yarn wrapping machine for environmentally friendly knitted fabrics and storage devices; image 3 Is the parameter map of the yarn covering machine
Login to View More If you want an in-depth research or a technical report, you can always get what you want in Patsnap Eureka TechResearch . Try now!