Research on the flexibility properties and applications of HDPE (High-Density Polyethylene) - Eureka
HDPE Flexibility Properties and Goals
This section will explore the key factors contributing to HDPE's flexibility, such as its molecular structure, crystallinity, and processing conditions. Additionally, it will highlight the diverse range of applications where HDPE's flexibility is leveraged, including packaging, construction, automotive, and consumer goods. The analysis will also consider the potential challenges and limitations associated with HDPE's flexibility, as well as emerging trends and innovations in enhancing its performance.
Market Demand for Flexible HDPE Applications
- Growing Demand for Flexible HDPE Products
The market for flexible HDPE applications is expanding rapidly, driven by the increasing need for lightweight, durable, and cost-effective materials in various industries, such as packaging, construction, and automotive. - Diverse Applications
Flexible HDPE products find applications in a wide range of sectors, including:- Packaging: Films, bags, and containers for food, beverages, and consumer goods
- Construction: Geomembranes, pipes, and insulation materials
- Automotive: Interior and exterior components, such as door panels and bumpers
- Market Drivers
Key factors fueling the demand for flexible HDPE applications include:- Sustainability and environmental concerns, leading to a shift towards recyclable and lightweight materials
- Cost-effectiveness and ease of processing compared to alternative materials
- Increasing urbanization and infrastructure development, particularly in emerging economies
- Market Trends and Projections
The global market for flexible HDPE applications is projected to experience significant growth in the coming years, driven by factors such as:- Advancements in HDPE formulations and processing technologies, enabling new applications
- Increasing demand for lightweight and durable materials in the automotive and construction sectors
- Regulatory initiatives promoting the use of sustainable and recyclable materials
Current State and Challenges of HDPE Flexibility
- Current Flexibility Limitations
HDPE exhibits relatively low flexibility compared to other polymers, which restricts its applications in areas requiring high elasticity or deformation. - Brittleness at Low Temperatures
HDPE becomes brittle and prone to cracking at low temperatures, limiting its use in cold environments or applications involving thermal cycling. - Challenges in Blending and Compounding
Achieving desired flexibility through blending or compounding with other polymers or additives can be challenging due to compatibility and processing issues. - Degradation and Aging Effects
Long-term exposure to environmental factors like heat, UV radiation, and chemicals can lead to degradation and embrittlement, reducing the flexibility of HDPE over time.
Evolution of HDPE Flexibility Technologies
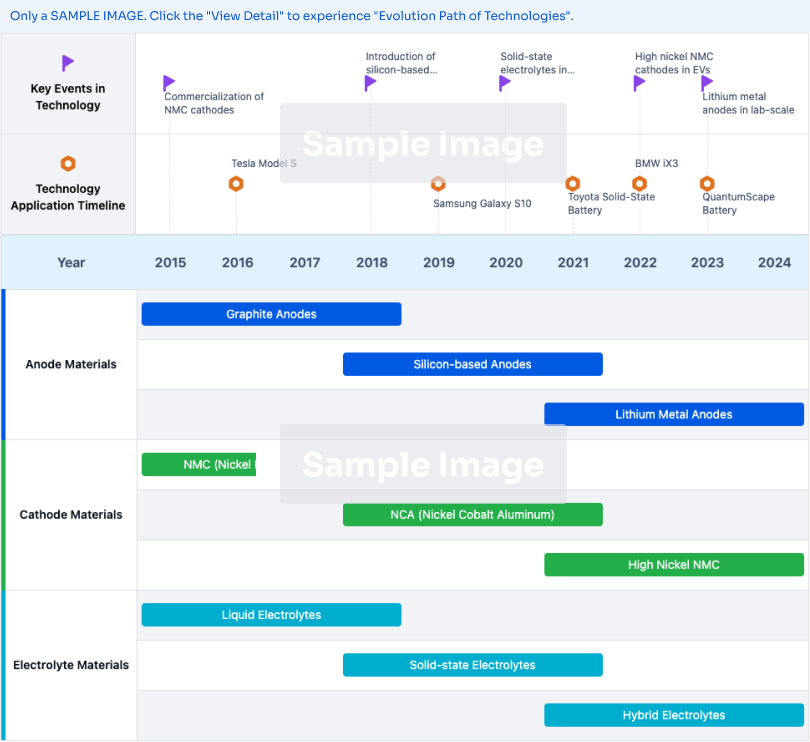
Existing Solutions for Enhancing HDPE Flexibility
01 HDPE Composite Materials
Composite materials are developed by combining HDPE with other materials to enhance properties like strength, conductivity, or heat resistance. These composites can be used in applications requiring improved performance compared to pure HDPE.- HDPE Composite Materials: Composite materials based on HDPE are developed to enhance properties like mechanical strength, thermal resistance, electrical conductivity, or flame retardancy. These composites involve reinforcing HDPE with fibers, blending with other polymers, or incorporating additives like conductive fillers or flame retardants.
- HDPE Pipe and Tube Products: HDPE is widely used for producing pipes, tubes, and related products due to its durability and chemical resistance. Various types, including reinforced pipes, coiled pipes, threaded pipes, and pipes with improved impact resistance or water drainage capabilities, are developed for applications in construction, plumbing, and transportation.
- HDPE Film and Sheet Materials: HDPE can be processed into films and sheets with properties like aging resistance, high dielectric strength, antistatic properties, or antibacterial characteristics. These materials find applications in packaging, insulation, and industries requiring moisture barrier, electrical insulation, or antimicrobial protection.
- HDPE Alloys and Blends: HDPE can be alloyed or blended with other polymers, such as polypropylene (PP), low-density polyethylene (LDPE), or ethylene-propylene copolymers, to create materials with tailored properties like improved impact resistance or flexibility for specific applications.
- HDPE Processing and Manufacturing Methods: Various processing and manufacturing methods, including extrusion, foaming, winding, and reinforcement techniques, are developed for HDPE products to improve production efficiency, quality, or performance of pipes, films, or composite materials.
02 HDPE Pipe and Tube Structures
HDPE is widely used for producing pipes, tubes, and related structures due to its durability and chemical resistance. Various designs and manufacturing processes are developed to improve strength, flexibility, and performance for different applications.03 HDPE Film and Membrane Materials
HDPE is used for producing films and membranes for applications like packaging, waterproofing, and insulation. Techniques are developed to enhance properties like aging resistance, antioxidant properties, and high-temperature resistance.04 HDPE Alloys and Blends
HDPE is combined with other polymers like polypropylene (PP) or low-density polyethylene (LDPE) to create alloys or blends with improved properties like fire resistance, antistatic behavior, or foaming characteristics.05 HDPE Processing and Manufacturing Techniques
Various techniques and methods are developed for processing and manufacturing HDPE products, like winding reinforcement, extrusion, foaming, and recycling processes, to improve efficiency, quality, and sustainability.
Key Players in HDPE Industry
Borealis AG
Dow Global Technologies LLC
Core Innovations in HDPE Flexibility
- Improved high density polyethylene (HDPE) specifically designed for manufacturing closures and caps, suitable for carbonated or still beverages.
- The HDPE composition is optimized for producing closures and caps with desirable properties.
- The invention provides closures and caps made from the improved HDPE composition, as well as their use.