Research on hybrid composite reinforcement for improving mechanical properties - Eureka
OCT 8, 20243 MIN READ
Generate Your Technical Report in Patsnap Eureka
AI-Powered Innovation Solution Platform for R&D
Hybrid Composite Reinforcement Goals and Background
The primary objective is to investigate and develop hybrid composite reinforcement techniques for enhancing the mechanical properties of materials. This involves combining different types of reinforcing fibers or fillers with a matrix material to create a synergistic effect, resulting in improved strength, stiffness, toughness, and other desirable properties.
Key areas of focus include optimizing the composition and arrangement of the reinforcement components, exploring novel material combinations, and developing efficient manufacturing processes. Potential applications span various industries, such as aerospace, automotive, construction, and sports equipment, where lightweight and high-performance materials are in demand.
Key areas of focus include optimizing the composition and arrangement of the reinforcement components, exploring novel material combinations, and developing efficient manufacturing processes. Potential applications span various industries, such as aerospace, automotive, construction, and sports equipment, where lightweight and high-performance materials are in demand.
Market Demand for Enhanced Mechanical Properties
- Increasing Demand for Lightweight Materials
There is a growing need for materials with enhanced mechanical properties, particularly in industries like aerospace, automotive, and construction, where weight reduction is crucial for improving efficiency and reducing environmental impact. - Improved Performance and Durability
Products with superior mechanical properties, such as higher strength, stiffness, and resistance to wear and corrosion, offer better performance and longer service life, leading to increased customer satisfaction and cost savings. - Emerging Applications
The development of materials with enhanced mechanical properties enables new applications in fields like renewable energy, biomedical devices, and advanced electronics, driving innovation and market growth. - Sustainability and Circular Economy
Materials with improved mechanical properties often have a longer lifespan, reducing the need for frequent replacements and contributing to a more sustainable and circular economy.
Current State and Challenges in Composite Reinforcement
- Composite Reinforcement Overview
Composites are engineered materials made from two or more constituents with different properties. Reinforcement is a crucial aspect, enhancing mechanical properties like strength and stiffness. - Current Challenges
Key challenges include achieving optimal fiber-matrix interface, improving impact resistance, reducing manufacturing costs, and addressing environmental concerns related to composite disposal. - Geographical Distribution
Major composite research and manufacturing hubs are located in North America, Europe, and Asia-Pacific regions, driven by aerospace, automotive, and construction industries.
Evolution of Hybrid Composite Technologies
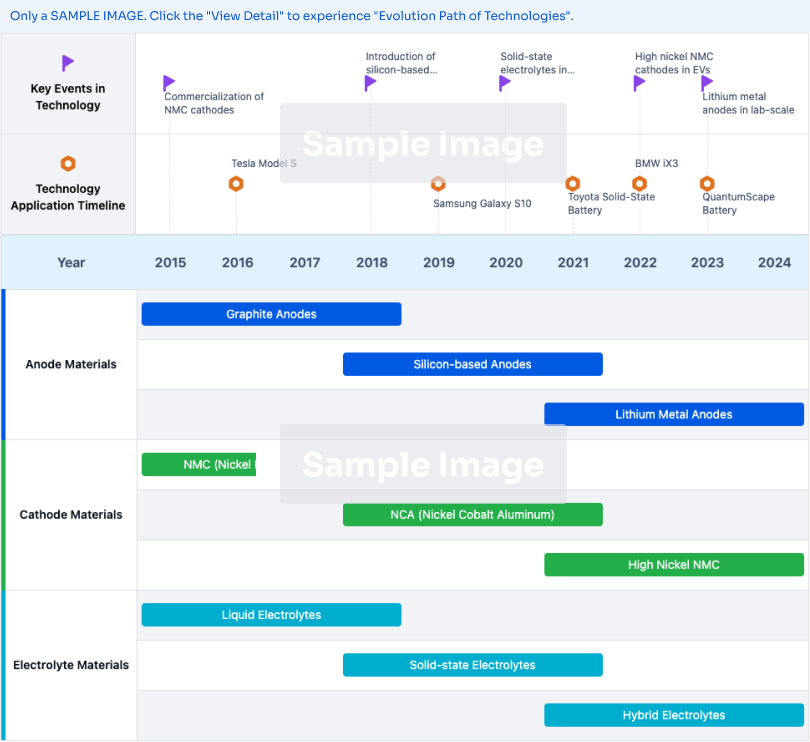
Existing Solutions for Composite Reinforcement
01 Fiber-reinforced Hybrid Composites
Hybrid composites can be formed by incorporating different types of fibers, such as glass, carbon, and natural fibers, into a polymer matrix. This combination enhances mechanical properties like strength, stiffness, and impact resistance.- Fiber-reinforced Hybrid Composites: Hybrid composites can be formed by incorporating different types of fibers, such as glass, carbon, and natural fibers, into a polymer matrix. This combination enhances mechanical properties like strength, stiffness, and impact resistance.
- Nanofiller-reinforced Hybrid Composites: Nanofillers like carbon nanotubes, graphene, and nanoparticles can be incorporated into polymer matrices to create hybrid composites with improved mechanical properties, including enhanced strength, stiffness, and toughness.
- Metal-reinforced Hybrid Composites: Hybrid composites can be formed by combining metal components with polymer matrices or other reinforcements. The metal components provide additional strength and stiffness, while the polymer matrix or other reinforcements contribute to properties like impact resistance or thermal insulation.
- Hierarchical Hybrid Composites: Hybrid composites can be designed with hierarchical structures, where different reinforcements or fillers are incorporated at different scales or levels, leading to synergistic effects and improved mechanical properties compared to traditional composites.
- Biomedical Hybrid Composites: Hybrid composites can be developed for biomedical applications like implants or prosthetics by combining biocompatible materials with reinforcements to achieve desired mechanical properties and biocompatibility.
02 Nanofiller-reinforced Hybrid Composites
Nanofillers like carbon nanotubes, graphene, and nanoparticles can be incorporated into polymer matrices to create hybrid composites with improved mechanical properties, including enhanced strength, stiffness, and toughness.03 Metal-reinforced Hybrid Composites
Hybrid composites can be formed by combining metal components with polymer or ceramic matrices, improving mechanical properties like strength and stiffness while providing lightweight and corrosion resistance.04 Hierarchical Hybrid Composites
Hybrid composites can be designed with hierarchical structures, where different materials or reinforcements are incorporated at different scales, leading to improved mechanical properties by combining advantages of different materials and structures.05 Application-specific Hybrid Composites
Hybrid composites can be tailored for specific applications like biomedical implants, aerospace components, or automotive parts by selecting appropriate materials and reinforcements to meet required mechanical and functional properties.
Key Players in Composite Material Industry
The competitive landscape for hybrid composite reinforcement to improve mechanical properties involves educational institutions and companies at various stages of technological maturity. Key players include Harbin Institute of Technology, Nanjing University of Aeronautics & Astronautics, and Massachusetts Institute of Technology, leading research efforts. Companies like Continental Reifen Deutschland GmbH, LX Hausys Ltd., and Toyota Motor Corp. are advancing practical applications. The market is growing, driven by demand in aerospace, automotive, and construction sectors, with contributions from academia and industry.
Harbin Institute of Technology
Technical Solution: Harbin Institute of Technology integrates carbon fibers and nanomaterials to enhance mechanical properties, focusing on optimizing the fiber-matrix interface and improving nanomaterial dispersion.
Strength: Advanced research capabilities. Weakness: Limited industrial applications.
Nanjing University of Aeronautics & Astronautics
Technical Solution: Nanjing University of Aeronautics & Astronautics combines carbon fibers and ceramic particles to improve mechanical strength and thermal stability for aerospace applications.
Strength: Strong focus on aerospace applications. Weakness: High production costs.
Core Innovations in Hybrid Composite Reinforcement
A method to identify the mechanical properties of surface treated natural fiber-PLA based green composites
PatentPendingIN202311024570A
Innovation
- Developing hybrid composites by combining different reinforcements
- Investigating the effect of hybrid reinforcements on mechanical properties
- Proposing different ways to improve the mechanical properties of the developed composites
Environmental Impact of Hybrid Composites
Hybrid composite reinforcement involves incorporating multiple types of reinforcing materials into a matrix to enhance mechanical properties. This technology aims to leverage the synergistic effects of different reinforcements, such as fibers, particles, and nanofillers, to improve strength, stiffness, and toughness. The key challenge lies in optimizing the composition, dispersion, and interfacial bonding of the reinforcements within the matrix. Potential innovations include developing novel reinforcement architectures, exploring advanced manufacturing techniques, and investigating multifunctional composites with tailored properties for specific applications.
the structure of the environmentally friendly knitted fabric provided by the present invention; figure 2 Flow chart of the yarn wrapping machine for environmentally friendly knitted fabrics and storage devices; image 3 Is the parameter map of the yarn covering machine
Login to View More Regulatory Standards for Composite Materials
Hybrid composite reinforcement involves incorporating multiple types of reinforcing materials into a matrix to enhance mechanical properties. This technology aims to leverage the synergistic effects of different reinforcements, such as fibers, particles, and nanofillers, to improve strength, stiffness, and toughness. The key challenge lies in optimizing the composition, dispersion, and interfacial bonding of the reinforcements within the matrix. Potential innovations include developing novel reinforcement architectures, exploring advanced manufacturing techniques, and investigating multifunctional composites with tailored properties for specific applications.
the structure of the environmentally friendly knitted fabric provided by the present invention; figure 2 Flow chart of the yarn wrapping machine for environmentally friendly knitted fabrics and storage devices; image 3 Is the parameter map of the yarn covering machine
Login to View More If you want an in-depth research or a technical report, you can always get what you want in Patsnap Eureka TechResearch . Try now!