Pulse Electroforming Technology - Eureka
OCT 10, 20243 MIN READ
Generate Your Technical Report in Patsnap Eureka
AI-Powered Innovation Solution Platform for R&D
Pulse Electroforming Technology Background and Goals
The primary objective of this section is to provide a comprehensive overview of the development history and evolution trends in the field of pulse electroforming technology. It should clearly outline the expected technological goals to be achieved. Key points to cover include:
Tracing the origins and major milestones in the development of pulse electroforming, highlighting the driving forces and motivations behind its advancement. Analyzing the current state of the technology and identifying the key challenges and limitations that need to be addressed. Discussing the potential future directions and anticipated breakthroughs that could shape the trajectory of this technology, based on emerging trends and research frontiers.
Tracing the origins and major milestones in the development of pulse electroforming, highlighting the driving forces and motivations behind its advancement. Analyzing the current state of the technology and identifying the key challenges and limitations that need to be addressed. Discussing the potential future directions and anticipated breakthroughs that could shape the trajectory of this technology, based on emerging trends and research frontiers.
Market Demand for Pulse Electroforming Applications
- Diverse Applications
Pulse electroforming finds applications across various industries, including aerospace, automotive, electronics, and medical devices. Its ability to produce intricate and precise components makes it suitable for manufacturing complex parts. - Demand for Lightweight Materials
The growing demand for lightweight yet strong materials in industries like aerospace and automotive is driving the market for pulse electroforming. This technology enables the production of lightweight components with high strength-to-weight ratios. - Miniaturization Trend
The trend towards miniaturization in electronics and medical devices is fueling the need for pulse electroforming. This technology allows for the fabrication of miniature components with intricate geometries and high precision. - Customization and Prototyping
Pulse electroforming facilitates rapid prototyping and customization, making it attractive for industries that require small-batch production or specialized components. - Replacement of Traditional Manufacturing
As a cost-effective and efficient alternative to traditional manufacturing methods, pulse electroforming is gaining traction in various industries, particularly for complex or high-precision components.
Current State and Challenges in Pulse Electroforming
- Current Limitations
Pulse electroforming technology faces several challenges, including:
- Difficulty in controlling pulse parameters for complex geometries
- Limited understanding of pulse-material interactions
- Lack of standardized process parameters for different materials
- Technical Hurdles
Key technical hurdles include:
- Achieving uniform thickness and properties across complex shapes
- Minimizing defects like porosity and cracking
- Improving deposition rates and efficiency
- Geographical Distribution
Pulse electroforming research is concentrated in:
- USA and Europe for aerospace and electronics applications
- China and Japan for manufacturing and tooling applications
Evolution of Electroforming Techniques
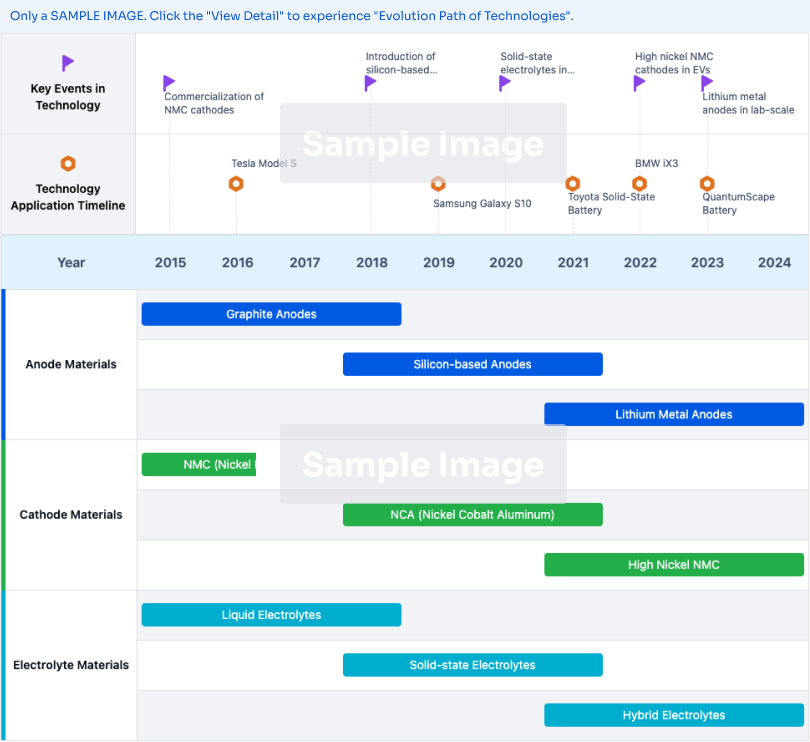
Existing Pulse Electroforming Solutions
01 Electroforming Devices and Apparatus
Various devices and apparatus designed for efficient and controlled electroforming operations, with specific configurations and components to facilitate the process.- Electroforming Devices and Apparatus: Various devices and apparatus designed for efficient and controlled electroforming operations, with specific configurations and components to facilitate the process.
- Electroforming Methods and Processes: Different methods and processes involving specific techniques, parameters, or steps to achieve desired electroforming results or improve the overall process.
- Pulse Electroforming Techniques: Techniques utilizing pulsed electrical signals or currents in the electroforming process, offering advantages like improved control, efficiency, or quality of the electroformed products.
- Electroforming Molds and Matrices: Specific molds, matrices, or mandrels designed and utilized for electroforming processes, serving as the base or template for the electroformed products and influencing their shape, size, or characteristics.
- Electroforming Jigs and Fixtures: Specialized jigs and fixtures used to hold or position the workpiece or other components during electroforming operations, helping ensure proper alignment, support, or positioning for consistent and accurate results.
02 Electroforming Methods and Processes
Different methods and processes involving specific techniques, parameters, or steps to achieve desired electroforming results or improve the overall process.03 Pulse Electroforming Techniques
Techniques utilizing pulsed electrical signals or currents in the electroforming process, offering advantages like improved control, efficiency, or quality of the electroformed products.04 Electroforming Matrices and Molds
Specific matrices, molds, or patterns used to shape or define the electroformed products, with particular designs or features to facilitate the process or achieve desired product characteristics.05 Electroforming Jigs and Fixtures
Jigs, fixtures, or supporting structures used to hold or position the workpiece or components during electroforming, with specific designs or features to enable efficient and accurate operations.
Key Players in Electroforming Industry
The competitive landscape for Pulse Electroforming Technology is diverse, with a mix of academic institutions and commercial enterprises. The industry is growing, driven by advancements in precision manufacturing and medical applications. Companies like General Electric and Applied Materials lead in technological maturity, leveraging extensive R&D capabilities. Academic institutions contribute significantly to foundational research, while specialized firms focus on niche applications.
General Electric Company
Technical Solution: General Electric has developed advanced pulse electroforming technology for high-precision manufacturing, achieving superior surface finish and dimensional accuracy for aerospace and medical applications through precise control of pulse parameters.
Strengths: High precision, suitable for critical applications. Weaknesses: High cost, complex process control.
Shenzhen Suntak Multilayer PCB Co. Ltd.
Technical Solution: Shenzhen Suntak employs pulse electroforming to enhance the reliability and performance of high-density interconnect PCBs by improving the quality of copper deposition.
Strengths: Improved PCB reliability, high-quality copper deposition. Weaknesses: Primarily focused on PCB industry, less versatile.
Core Innovations in Pulse Electroforming
equipment FOR THE APPLICATION OF ELECTRICAL VOLTAGE PULSES OF VARIABLE AMPLITUDE, PERIOD AND WAVEFORM AND EFFECTIVENESS ANALYSIS FOR ELECTROPORATION TECHNIQUES IN GENETIC TRANSFECTION AND TREATMENT OF NEOPLASMS
PatentPendingBR102019018097A2
Innovation
- The equipment allows for combining various parametric possibilities, enabling targeting of specific cellular systems or regions for reversible (e.g. genetic transfection and electrochemotherapy) and irreversible (e.g. membrane destruction and tissue ablation) treatments.
- The equipment can be programmed to avoid accentuated muscular mechanical responses in the patient during electrochemotherapy by using protocols with a high repetition rate.
- The acquisition system allows for an unprecedented assessment of the effectiveness of the electropermeabilization treatment immediately after the treatment by monitoring changes in electrical characteristics like impedance.
Regulatory Landscape for Electroforming Technologies
Pulse electroforming technology, also known as pulse electrodeposition, is an advanced electroforming process that utilizes pulsed direct current (DC) instead of conventional constant DC. This technique offers several advantages, including improved material properties, enhanced deposition rate, and better control over the microstructure and composition of the deposited layer. The technology has applications in various industries, such as electronics, aerospace, and automotive, where precise and high-quality metal coatings are required. The report aims to provide a comprehensive overview of this technology, including its principles, current status, challenges, and future development directions.
the structure of the environmentally friendly knitted fabric provided by the present invention; figure 2 Flow chart of the yarn wrapping machine for environmentally friendly knitted fabrics and storage devices; image 3 Is the parameter map of the yarn covering machine
Login to View More Environmental Impact of Electroforming Processes
Pulse electroforming technology, also known as pulse electrodeposition, is an advanced electroforming process that utilizes pulsed direct current (DC) instead of conventional constant DC. This technology has gained significant attention due to its ability to produce high-quality metal coatings with improved properties compared to traditional electroforming methods. The pulsed current allows for better control over the deposition process, resulting in coatings with finer grain structure, higher hardness, and improved corrosion resistance. Additionally, pulse electroforming can be used to deposit a wide range of metals and alloys, making it suitable for various applications in industries such as aerospace, automotive, and electronics.
the structure of the environmentally friendly knitted fabric provided by the present invention; figure 2 Flow chart of the yarn wrapping machine for environmentally friendly knitted fabrics and storage devices; image 3 Is the parameter map of the yarn covering machine
Login to View More If you want an in-depth research or a technical report, you can always get what you want in Patsnap Eureka TechResearch . Try now!