Research on Catalytic Process Intensification - Eureka
Catalytic Process Background and Objectives
Additionally, it will outline the anticipated technological goals and targets that catalytic process intensification aims to achieve, shedding light on the desired outcomes and potential applications driving further research and development efforts in this field.
Market Demand for Catalytic Process Intensification
- Market Size and Growth
Catalytic process intensification has a vast potential market, driven by the need for energy efficiency and sustainability across various industries. The market size is projected to grow significantly due to increasing environmental regulations and the demand for optimized processes. - Industry Adoption
The adoption of catalytic process intensification is expected to be widespread across chemical, petrochemical, pharmaceutical, and energy sectors. These industries are continuously seeking ways to enhance process efficiency, reduce energy consumption, and minimize environmental impact. - Cost Savings and Competitiveness
Implementing catalytic process intensification can lead to substantial cost savings through improved energy efficiency, reduced waste generation, and increased productivity. This can provide a competitive advantage for companies operating in highly competitive markets. - Environmental Benefits
The market demand is fueled by the environmental benefits associated with catalytic process intensification, such as reduced greenhouse gas emissions, lower energy consumption, and decreased waste generation. This aligns with the global push towards sustainable practices. - Regulatory Compliance
Stringent environmental regulations and emission standards are driving the demand for catalytic process intensification as a means to comply with regulatory requirements while maintaining operational efficiency.
Current State and Challenges in Catalytic Processes
- Catalyst Deactivation
Catalysts can deactivate over time due to various reasons, such as poisoning, fouling, sintering, and phase transformation, leading to reduced activity and selectivity. - Mass and Heat Transfer Limitations
Inefficient mass and heat transfer can limit the overall reaction rate and catalyst utilization, resulting in lower productivity and energy efficiency. - Reactor Design Challenges
Conventional reactor designs may not be optimized for specific catalytic processes, leading to suboptimal performance and scalability issues. - Catalyst Synthesis and Characterization
Developing highly active, selective, and stable catalysts with desired properties remains a significant challenge, requiring advanced synthesis and characterization techniques. - Process Intensification Barriers
Implementing process intensification strategies, such as micro-reactors or membrane reactors, can be hindered by technical and economic barriers, including material compatibility and scalability concerns.
Evolution of Catalytic Process Technologies
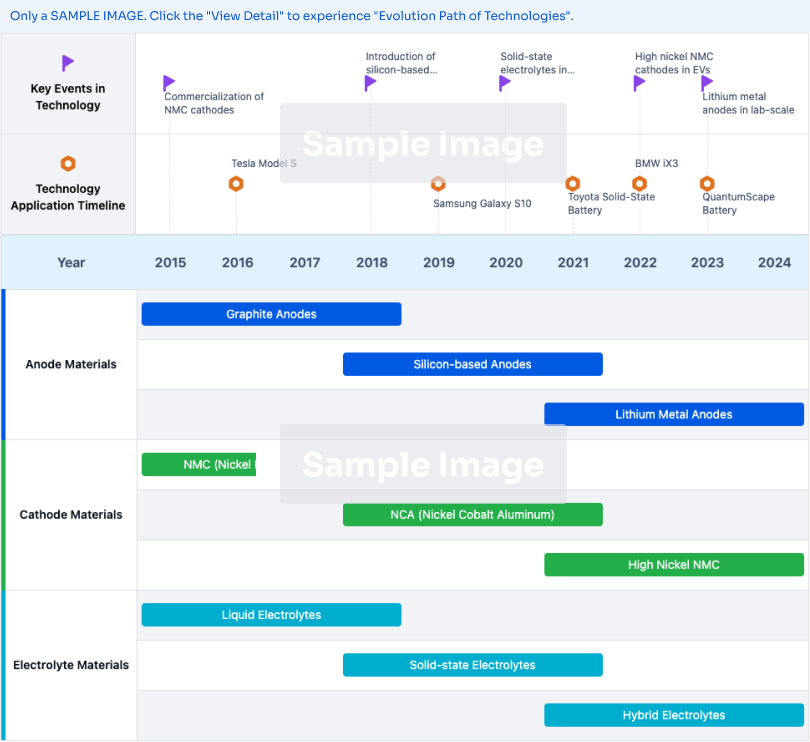
Existing Solutions for Catalytic Process Intensification
01 Catalytic Reaction Process Intensification
Compact catalytic membrane reactors, integrated reaction-separation, and hydrodynamic cavitation reactors enhance efficiency, productivity, and sustainability.- Catalytic Reaction Process Intensification: Techniques like compact catalytic membrane reactors, integrated reaction-separation, and hydrodynamic cavitation reactors enhance efficiency, productivity, and sustainability.
- Catalytic Cracking Process Intensification: Integrated staged cracking and hydroprocessing, high-efficiency stripping, modeling, and specialized reactor designs improve product yields, energy efficiency, and process control.
- Catalytic Reforming Process Intensification: Multi-stage ebullated bed reactors, specialized designs, and process integration enhance efficiency, product quality, and hydrogen production in catalytic reforming.
- Catalytic Hydrogenation Process Intensification: Multi-stage ebullated bed reactors, specialized designs, and process integration improve efficiency, selectivity, and product quality in catalytic hydrogenation.
- Catalytic Conversion and Upgrading Intensification: Techniques like crude oil direct catalytic upgrading, biomass-derived liquid hydroprocessing, and catalytic dehydrogenation improve product yields, energy efficiency, and sustainability.
02 Catalytic Cracking Process Intensification
Process modeling, reactor design optimization, and specialized reactors or integrated systems improve cracking efficiency, product yields, and process economics.03 Catalytic Reforming Process Intensification
Multi-stage ebullated bed reactors, integrated reaction-rectification systems, and process optimization improve product yields and energy efficiency.04 Catalytic Hydroprocessing Intensification
Catalyst formulations, reactor designs, and process configurations enhance efficiency, selectivity, and product quality in hydroprocessing reactions.05 Catalytic Process Modeling and Optimization
Computational modeling, optimization techniques, and artificial intelligence improve reactor performance and process control.
Key Players in Catalytic Process Industry
China Petroleum & Chemical Corp.
ExxonMobil Chemical Patents, Inc.
Core Innovations in Catalytic Process Technologies
- Developing a series of PolyHIPEs with different combinations of monomers like thiols, cyclic and aliphatic alkenes and alkynes to screen materials conducive for providing catalytic excellence, chemical insusceptibility, and mechanical endurance.
- Integrating PolyHIPE-immobilized catalysts with dynamically stirred continuous flow reactors like Agitated Cell Reactor (ACR) or Agitated Tube Reactor (ATR) for intensification of heterogeneous catalytic processes.
- Addressing challenges of conventional fixed-bed and fluidized-bed reactors by using PolyHIPE-immobilized catalysts in continuous flow reactors.
Future Directions in Catalytic Process Intensification
- Membrane Reactors
- Microreactors
- Process Intensification by Reactive Distillation