Research on the development and application of Vacuum Insulation Panels (VIPs) - Eureka
VIP Technology Background and Objectives
Additionally, it will clearly define the expected technological goals and performance targets that VIPs aim to achieve, outlining the desired outcomes and potential applications driving further research and development efforts in this domain.
Market Demand for Vacuum Insulation Panels
- Growing Demand
Vacuum insulation panels (VIPs) are witnessing a surge in demand due to their exceptional thermal insulation properties and space-saving advantages. The construction industry is a major driver, as VIPs enable thinner walls and roofs while meeting stringent energy efficiency standards. - Energy Efficiency Regulations
Tightening energy efficiency regulations and building codes are propelling the adoption of VIPs in both residential and commercial construction projects. Governments worldwide are promoting energy-efficient building practices, creating a favorable market environment for VIPs. - Cold Chain and Logistics
The cold chain and logistics sectors are increasingly utilizing VIPs to maintain desired temperature ranges during transportation and storage of temperature-sensitive goods, such as pharmaceuticals, food, and beverages. - Appliance and Equipment Insulation
VIPs are finding applications in insulating refrigerators, freezers, and other appliances, as well as in industrial equipment and machinery, where space constraints and high insulation performance are critical. - Emerging Applications
Innovative applications of VIPs are emerging in areas like automotive insulation, protective packaging, and wearable technology, driven by the demand for lightweight, compact, and highly efficient insulation solutions.
Current State and Challenges of VIPs
- Current Technological Limitations
VIPs face challenges in maintaining vacuum over long periods, as gas permeation through the envelope and outgassing from core materials can degrade insulation performance. - Manufacturing Complexities
Producing VIPs with consistent quality and performance is difficult due to the stringent requirements for vacuum levels, envelope sealing, and core material processing. - Material Constraints
The selection of suitable core materials and envelope materials is limited, as they must meet specific criteria for low thermal conductivity, low gas permeability, and compatibility with vacuum conditions. - Aging and Degradation Issues
Over time, VIPs can experience aging effects, such as gas permeation, material degradation, and loss of vacuum, leading to reduced insulation performance. - Geographic Distribution Challenges
The production and application of VIPs are concentrated in certain regions, with limited availability and adoption in other parts of the world, hindering widespread implementation.
Evolution Path of Vacuum Insulation Technology
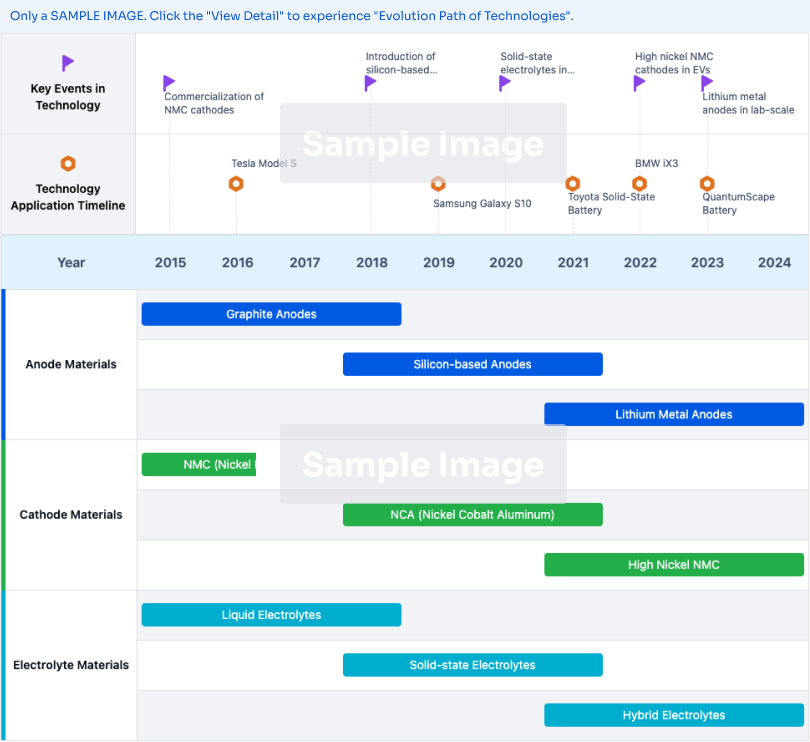
Current Solutions for VIP Implementation
01 VIP Structure and Composition
The results cover the use of different core materials like opacified powders or fibers, and protective skins or coatings to prevent air leakage and maintain the vacuum within the panels.- VIP Structure and Composition: The results cover different core materials, like multi-layer, polymer-coated, and graduated density cores, to enhance thermal insulation. Reinforcing elements like steel meshes and edge insulation techniques to reduce thermal bridging are also discussed.
- Thermal Insulation Performance Evaluation: Methods and equipment for evaluating thermal insulation performance, such as guarded hot plate method, rapid testing devices, and equipment for vacuum glass production lines, are covered.
- Building and Construction Applications: VIPs are used in external thermal insulation systems, insulation layers for walls and roofs, and thermal insulation for steel structures. Composite insulation solutions with polyurethane foam and construction methods for integrating VIPs are discussed.
- Thermal Insulation Containers and Vessels: The integration of VIPs in insulation systems of refrigerators, thermal insulation boxes, and storage containers, along with their production methods and materials, is covered.
- Fireproofing and Thermal Protection: The preparation methods and materials for enhancing fire resistance and thermal protection capabilities of VIPs in applications like fireproof vacuum insulation panels for building external thermal insulation systems are addressed.
02 Thermal Insulation Performance Evaluation
Methods and equipment for evaluating thermal conductivity, heat transfer, insulation effectiveness, and rapid testing devices for improving accuracy are covered.03 Building Insulation Systems Integration
The integration of VIPs into building insulation systems like exterior and interior wall insulation, insulation for specific components, construction methods, layer configurations, and thermal bridging reduction techniques are discussed.04 Thermal Insulation in Containers and Appliances
The use of VIPs for thermal insulation in refrigerators, thermal insulation boxes, wine insulation cans, and the design and construction of insulated containers using VIPs are covered.05 Fireproofing and Edge Insulation
The development of fireproof VIPs for building insulation systems, and techniques for improving edge insulation and reducing thermal bridging at the edges of VIPs are addressed.
Key Players in VIP Industry
Fujian SuperTech Advanced Material Co., Ltd.
Kingspan Research & Developments Ltd.
Core Innovations in VIP Technology
- Utilizing two thin metal foil pieces welded together to form a sealed and evacuated enclosure for the vacuum insulation panel core
- Incorporating a molecule-absorbing getter inside the evacuated enclosure to maintain the vacuum
- A novel manufacturing process involving clamping, evacuating, and welding the metal foil enclosure
Future Directions for VIP Research
- Aerogel-based VIPs
- Hybrid VIPs with Multilayer Structures
- Advanced Envelope Materials and Sealing Technologies