Research on improving corrosion resistance of materials - Eureka
Corrosion Resistance Technology Background and Goals
Key areas of focus include developing advanced coatings, surface treatments, and corrosion-resistant alloys. Innovative approaches, such as incorporating nanostructured materials, self-healing coatings, and bio-inspired designs, hold promising potential for achieving superior corrosion resistance. Ongoing research efforts aim to address the challenges posed by different corrosion mechanisms, environmental conditions, and material requirements across diverse industries.
Market Demand for Corrosion Resistant Materials
- Growing Demand
The demand for corrosion-resistant materials is steadily increasing across various industries, driven by the need for longer-lasting and more durable products, as well as stricter environmental regulations. - Infrastructure and Construction
Corrosion-resistant materials are crucial for infrastructure projects, such as bridges, pipelines, and buildings, to ensure structural integrity and longevity, reducing maintenance costs and enhancing safety. - Automotive and Transportation
The automotive and transportation sectors require corrosion-resistant materials for vehicle bodies, components, and equipment to withstand harsh environmental conditions and extend service life. - Energy and Chemical Processing
The energy and chemical processing industries rely on corrosion-resistant materials for equipment, pipelines, and storage tanks to prevent leaks, maintain efficiency, and ensure safe operations. - Marine and Offshore
Corrosion-resistant materials are essential for marine and offshore applications, such as ships, offshore platforms, and coastal structures, to protect against seawater corrosion and harsh marine environments.
Current State and Challenges in Corrosion Resistance
- Current Challenges
Corrosion remains a significant issue across various industries, leading to substantial economic losses and safety concerns. Existing corrosion prevention methods often have limitations in terms of effectiveness, durability, and environmental impact. - Material Limitations
Traditional materials like metals and alloys are susceptible to corrosion, especially in harsh environments. Their inherent properties can restrict their corrosion resistance capabilities. - Environmental Factors
Corrosion is influenced by various environmental factors, such as temperature, humidity, pH levels, and the presence of corrosive substances. These factors can accelerate corrosion processes and pose challenges for material protection. - Complex Mechanisms
Corrosion involves intricate electrochemical and physical processes, making it difficult to fully understand and control. The interplay between materials, environments, and corrosion mechanisms complicates the development of effective solutions. - Maintenance and Monitoring
Continuous monitoring and maintenance are often required to detect and mitigate corrosion, which can be time-consuming and costly, especially in remote or inaccessible locations.
Evolution of Corrosion Resistant Materials
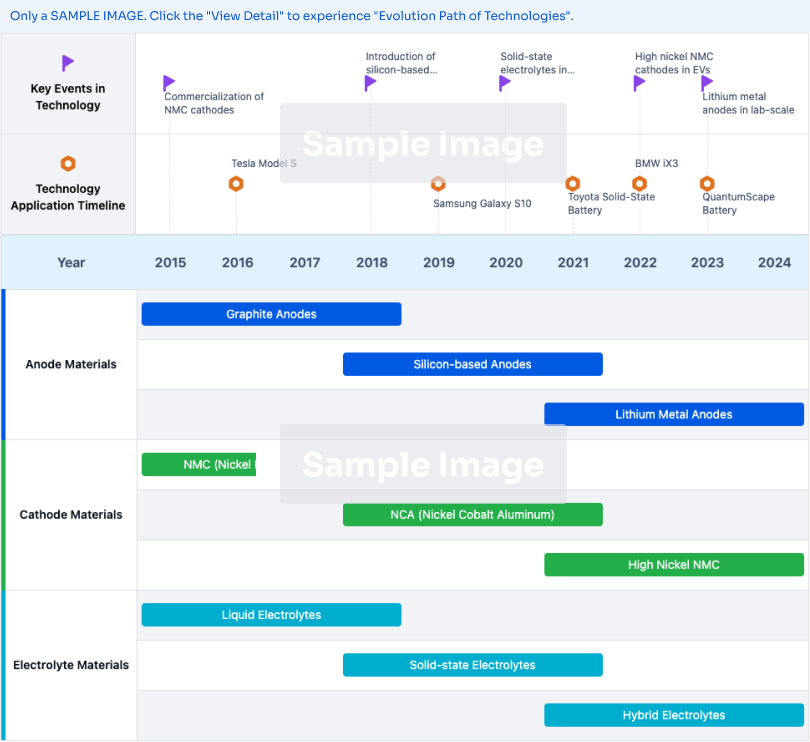
Existing Solutions for Corrosion Resistance
01 Corrosion Resistance Evaluation Methods
Various methods have been developed to evaluate the corrosion resistance of materials, including accelerated corrosion tests, electrochemical techniques, and simulated environmental exposure tests. These methods aim to assess the material's resistance to different types of corrosion, such as pitting, crevice, and stress corrosion cracking.- Corrosion Resistance Evaluation Methods: Various methods have been developed to evaluate the corrosion resistance of materials, including accelerated corrosion tests, electrochemical techniques, and simulated environmental exposure tests. These methods assess the material's resistance to different types of corrosion, such as pitting, crevice, and stress corrosion cracking.
- Corrosion-Resistant Alloy Compositions: Certain alloy compositions have been developed to enhance the corrosion resistance of materials, particularly in harsh environments. These alloys may contain specific elements or combinations of elements that improve resistance to various forms of corrosion, such as chloride-induced corrosion, stress corrosion cracking, and atmospheric corrosion.
- Surface Treatments for Corrosion Resistance: Various surface treatments have been developed to improve the corrosion resistance of materials. These treatments can involve coating, plating, or modifying the surface layer of the material to enhance its resistance to corrosion, such as chromate conversion coatings, anodizing, and nitriding processes.
- Corrosion Resistance of Coated Materials: Coatings can be applied to materials to enhance their corrosion resistance. These coatings can act as a barrier against corrosive environments or provide sacrificial protection. Evaluation methods have been developed to assess the corrosion resistance of coated materials under various conditions.
- Corrosion Resistance in Specific Applications: Certain materials and treatments have been developed to address corrosion resistance requirements in specific applications, such as dental materials, aerospace materials, grounding materials, and welded joints. These solutions aim to provide corrosion protection tailored to the unique conditions and environments encountered in these applications.
02 Corrosion-Resistant Alloy Compositions and Materials
Specific alloy compositions and materials have been developed to enhance corrosion resistance, particularly for applications in harsh environments. These materials may incorporate elements like chromium, nickel, or molybdenum to improve their resistance to various forms of corrosion, such as general corrosion, pitting, and stress corrosion cracking.03 Surface Treatments for Improving Corrosion Resistance
Various surface treatments have been developed to enhance the corrosion resistance of materials. These treatments can involve coating, plating, or modifying the surface layer of the material to create a protective barrier or improve its chemical and physical properties, thereby increasing its resistance to corrosion.04 Corrosion Resistance Evaluation for Coated Materials
Specific methods and techniques have been developed to evaluate the corrosion resistance of coated materials, such as painted or coated metal surfaces. These methods aim to assess the effectiveness of the coating in protecting the underlying material from corrosion and may involve accelerated testing or simulated environmental exposure.05 Corrosion Resistance in Specific Environments or Applications
Certain materials and methods have been developed to address corrosion resistance in specific environments or applications, such as high-temperature, high-pressure, or microbial environments. These materials and methods aim to provide enhanced corrosion resistance under the unique conditions encountered in these applications.
Key Players in Corrosion Resistance Industry
Core Innovations in Corrosion Resistant Materials
- The use of a water-containing material to remove the surface treatment film and adherents, allowing for easy and reliable removal of the adherents.
- The application of a constant current between the metal base and the water-containing material, or between the two electrodes, ensuring stability in the treatment process.
- The combination of the damaged portion treatment method with the corrosion resistance test for a coated metal material, allowing for a highly reliable evaluation of the corrosion resistance of the coated metal material.