Research on improving the wear resistance of HDPE (High-Density Polyethylene) - Eureka
OCT 8, 20244 MIN READ
Generate Your Technical Report in Patsnap Eureka
AI-Powered Innovation Solution Platform for R&D
HDPE Wear Resistance Challenges and Goals
The primary objective is to enhance the wear resistance of high-density polyethylene (HDPE), a widely used thermoplastic polymer known for its exceptional strength, durability, and chemical resistance. Improving wear resistance is crucial for extending the service life of HDPE products and expanding their applications in demanding environments.
Key areas of focus include modifying the polymer structure, incorporating reinforcing fillers or additives, and exploring surface treatment techniques. Potential solutions may involve optimizing the molecular weight distribution, introducing cross-linking agents, or incorporating nanoparticles or fibers to enhance the material's tribological properties. Additionally, surface treatments like plasma modification or coating could be explored to improve the surface hardness and wear resistance of HDPE components.
Key areas of focus include modifying the polymer structure, incorporating reinforcing fillers or additives, and exploring surface treatment techniques. Potential solutions may involve optimizing the molecular weight distribution, introducing cross-linking agents, or incorporating nanoparticles or fibers to enhance the material's tribological properties. Additionally, surface treatments like plasma modification or coating could be explored to improve the surface hardness and wear resistance of HDPE components.
Market Demand for Durable HDPE Products
- Growing Demand for Durable Plastics
The market for durable plastic products is expanding rapidly, driven by the need for lightweight, corrosion-resistant, and long-lasting materials in various industries, including construction, automotive, and consumer goods. - Advantages of HDPE
High-density polyethylene (HDPE) is a popular choice due to its exceptional strength, chemical resistance, and low maintenance requirements, making it suitable for applications where durability and longevity are crucial. - Key Applications
Major applications of durable HDPE products include:- Construction: Pipes, geomembranes, and liners for water and waste management
- Automotive: Fuel tanks, battery cases, and interior components
- Consumer goods: Storage containers, toys, and outdoor furniture
- Market Growth Drivers
The demand for durable HDPE products is fueled by factors such as:- Increasing infrastructure development and urbanization
- Growing emphasis on sustainability and eco-friendly materials
- Advancements in manufacturing processes and product design
- Regional Market Dynamics
The Asia-Pacific region is expected to dominate the market for durable HDPE products due to rapid industrialization and infrastructure growth, followed by North America and Europe.
Current State and Limitations of HDPE Wear Resistance
- Limited Wear Resistance
HDPE exhibits relatively low wear resistance compared to other engineering polymers, making it susceptible to abrasion, erosion, and surface damage in applications involving sliding or high-impact forces. - Dependence on Operating Conditions
The wear resistance of HDPE is highly dependent on factors such as temperature, load, sliding speed, and counterface material, making it challenging to predict and optimize its performance across various operating conditions. - Tribo-oxidative Degradation
HDPE undergoes tribo-oxidative degradation during wear, leading to the formation of oxidized species and chain scission, which further accelerates the wear process and compromises the material's mechanical properties. - Lack of Effective Additives
While various additives, such as fillers and lubricants, have been explored to enhance the wear resistance of HDPE, their effectiveness is often limited, and they may introduce undesirable side effects or compatibility issues.
Evolution of HDPE Wear Resistance Technologies
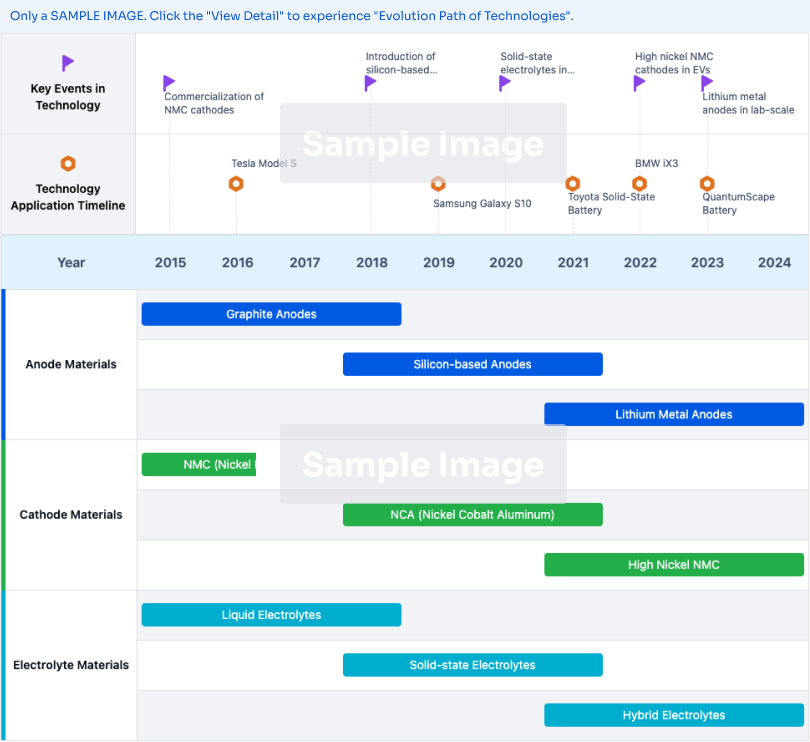
Existing Solutions for Enhancing HDPE Wear Resistance
01 Improving wear resistance by modifying HDPE
Enhancing wear resistance of HDPE through composition or structural modifications, such as incorporating reinforcing fillers, crosslinking agents, or other additives to improve mechanical properties and abrasion resistance.- Reinforced HDPE composites: Incorporating reinforcing materials like glass fibers, carbon fibers, or nanoparticles into HDPE to enhance wear resistance, mechanical properties, abrasion resistance, impact strength, and durability.
- Crosslinked HDPE: Applying crosslinking techniques to HDPE to create a three-dimensional network structure, resulting in improved wear resistance, chemical resistance, and mechanical properties for high durability and abrasion resistance applications.
- Impact and wear-resistant composites: Combining HDPE with other polymers or additives to create composite materials with enhanced impact resistance and wear resistance, designed for harsh environments and superior durability.
- Aging and weather-resistant HDPE: Modifying or formulating HDPE materials to improve resistance to aging, UV radiation, and weathering effects, maintaining mechanical properties and appearance for outdoor applications.
- Recycled HDPE for wear resistance: Recycling and reusing HDPE materials through techniques like thermofusion and blending with virgin HDPE to produce recycled products with improved wear resistance and durability.
02 Enhancing impact and wear resistance
Certain modifications to HDPE can simultaneously improve its impact resistance and wear resistance, involving specific additives, polymer blending, or altering processing conditions.03 Reinforced HDPE composites
Creating HDPE composites reinforced with fibers, meshes, or other reinforcing agents to enhance wear resistance for applications requiring high wear resistance.04 Tailored wear resistance
Adjusting HDPE composition, processing conditions, or incorporating specialized additives to achieve desired wear resistance for specific applications like water pipelines, chemical barrels, or automotive components.05 Recycled HDPE for wear resistance
Processing and modifying recycled HDPE to improve wear resistance, allowing reuse of waste materials in applications requiring high wear resistance.
Key Players in HDPE Industry
The competitive landscape for improving the wear resistance of HDPE involves established chemical companies and research institutions. The industry is mature with significant market size, driven by demand across various sectors. Key players like Borealis AG, SABIC Global Technologies BV, Dow Global Technologies LLC, and ExxonMobil Chemical Patents, Inc. have advanced R&D capabilities and market reach. Research institutions contribute to technological advancements, with ongoing innovations aimed at enhancing material properties.
Borealis AG
Technical Solution: Borealis AG's Borstar technology enhances HDPE wear resistance by optimizing polymer structure and incorporating advanced additives, widely used in applications requiring high durability.
Strength: Proven technology with wide application. Weakness: High cost of implementation.
SABIC Global Technologies BV
Technical Solution: SABIC uses nanocomposites to improve HDPE wear resistance by dispersing nanoparticles uniformly within the polymer matrix, enhancing mechanical properties.
Strength: Superior mechanical properties. Weakness: Complex manufacturing process.
Core Innovations in HDPE Wear Resistance
HIGH DENSITY polyethylene FOR COVERS AND CLOSURES
PatentInactiveBR112014007199A2
Innovation
- Improved high density polyethylene (HDPE) specifically designed for manufacturing closures and caps, suitable for carbonated or still beverages.
- The HDPE composition is optimized for producing closures and caps with enhanced properties.
- The invention provides closures and caps made from the improved HDPE composition, as well as their use.
Environmental Impact of HDPE Wear Resistance Enhancements
Here is a concise summary of the research report on improving the wear resistance of HDPE (High-Density Polyethylene), based on the provided directory:
High-density polyethylene (HDPE) is a widely used thermoplastic polymer known for its excellent chemical resistance, impact strength, and cost-effectiveness. However, its relatively low wear resistance limits its applications in areas where abrasion and friction are significant factors. This report explores various approaches to enhance the wear resistance of HDPE, including material modifications, surface treatments, and composite formulations. Key technologies discussed include reinforcement with nanoparticles, radiation-induced crosslinking, and the incorporation of lubricating additives. Potential innovations may involve developing self-lubricating HDPE composites or exploring novel surface engineering techniques to improve tribological properties. The report aims to provide insights into the current state of the art and future research directions for improving the wear performance of this versatile polymer.
the structure of the environmentally friendly knitted fabric provided by the present invention; figure 2 Flow chart of the yarn wrapping machine for environmentally friendly knitted fabrics and storage devices; image 3 Is the parameter map of the yarn covering machine
Login to View More Regulatory Landscape for HDPE Products
Here is a concise summary of the research report on improving the wear resistance of HDPE (High-Density Polyethylene), based on the provided directory:
High-density polyethylene (HDPE) is a widely used thermoplastic polymer known for its excellent chemical resistance, impact strength, and low cost. However, its relatively low wear resistance limits its applications in areas with high friction or abrasion. Improving HDPE's wear resistance has been a focus of research and development efforts. Various approaches have been explored, including reinforcement with fibers or nanoparticles, surface modification techniques, and the development of composite materials. Ongoing research aims to develop cost-effective and scalable solutions to enhance HDPE's tribological properties while maintaining its desirable characteristics. Potential innovations may involve novel material compositions, surface engineering methods, or manufacturing processes tailored for specific applications.
the structure of the environmentally friendly knitted fabric provided by the present invention; figure 2 Flow chart of the yarn wrapping machine for environmentally friendly knitted fabrics and storage devices; image 3 Is the parameter map of the yarn covering machine
Login to View More If you want an in-depth research or a technical report, you can always get what you want in Patsnap Eureka TechResearch . Try now!