Research on improving the impact resistance of HDPE (High-Density Polyethylene) - Eureka
OCT 8, 20244 MIN READ
Generate Your Technical Report in Patsnap Eureka
AI-Powered Innovation Solution Platform for R&D
HDPE Impact Resistance Goals and Background
The primary objective is to enhance the impact resistance of high-density polyethylene (HDPE), a widely used thermoplastic polymer known for its strength, durability, and chemical resistance. Improving the impact resistance of HDPE is crucial for applications where the material is subjected to high impact loads, such as in the construction, automotive, and packaging industries.
Several approaches have been explored to address this challenge, including the incorporation of impact modifiers, the use of nanofillers, and the development of polymer blends or composites. However, each method has its own limitations and trade-offs, necessitating further research and innovation to achieve optimal impact resistance while maintaining other desirable properties of HDPE.
Several approaches have been explored to address this challenge, including the incorporation of impact modifiers, the use of nanofillers, and the development of polymer blends or composites. However, each method has its own limitations and trade-offs, necessitating further research and innovation to achieve optimal impact resistance while maintaining other desirable properties of HDPE.
Market Demand for Impact-Resistant HDPE
- Growing Demand
Impact-resistant HDPE is witnessing a surge in demand across various industries, driven by its superior durability, lightweight, and cost-effectiveness compared to traditional materials like metals and glass. - Infrastructure Applications
The construction and infrastructure sectors are major consumers, utilizing impact-resistant HDPE for pipes, fittings, and protective linings due to its resistance to corrosion, chemicals, and abrasion. - Automotive Industry
The automotive industry is increasingly adopting impact-resistant HDPE for fuel tanks, interior components, and exterior trims, leveraging its impact resistance, lightweight, and recyclability. - Consumer Goods
Impact-resistant HDPE finds applications in consumer goods like storage containers, toys, and sports equipment, where durability and safety are paramount. - Emerging Markets
Developing regions with rapid urbanization and infrastructure development are driving the demand for impact-resistant HDPE, presenting significant growth opportunities.
Current State and Challenges in HDPE Impact Resistance
- Limited Impact Resistance
HDPE exhibits relatively low impact resistance compared to other polymers, making it susceptible to cracking or fracturing under sudden impacts or loads. - Environmental Factors
The impact resistance of HDPE can be affected by environmental conditions such as temperature, UV exposure, and chemical exposure, leading to degradation and reduced performance. - Processing Challenges
The processing methods used to manufacture HDPE products, such as injection molding or extrusion, can influence the material's impact resistance, with improper processing parameters leading to defects or weaknesses. - Structural Limitations
The semi-crystalline structure of HDPE can limit its ability to absorb and dissipate impact energy effectively, resulting in brittle failure modes under certain loading conditions.
Evolution of HDPE Impact Resistance Technologies
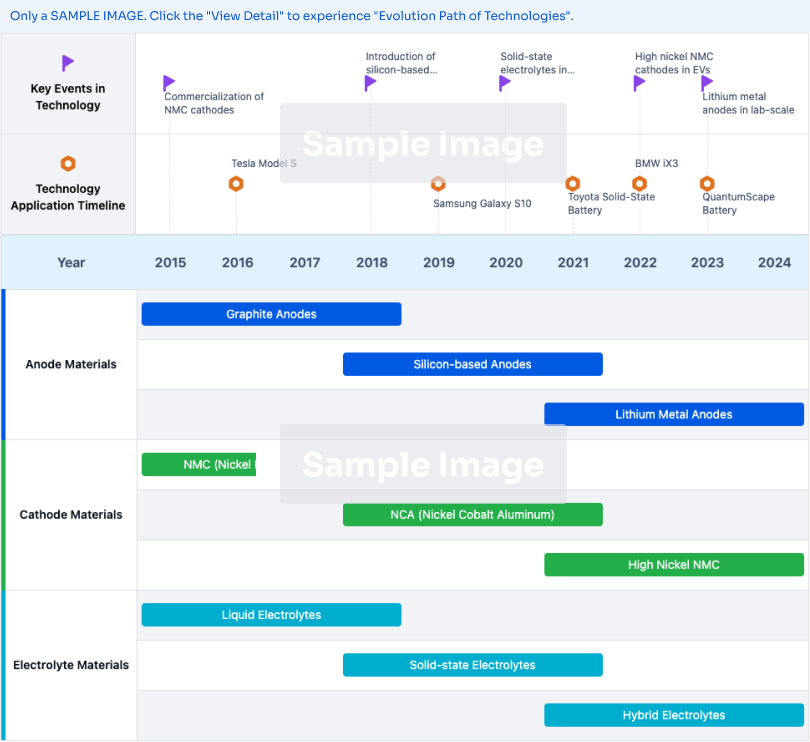
Existing Solutions for HDPE Impact Resistance
01 High Impact Resistance HDPE Materials
Various HDPE materials have been developed to enhance impact resistance, incorporating reinforcements, fillers, or specific polymer blends to improve the impact strength of HDPE products.- High Impact Resistance HDPE Materials: Various methods and compositions are disclosed for enhancing the impact resistance of high-density polyethylene (HDPE) materials, including blending HDPE with other polymers, reinforcing with fibers or nanoparticles, or modifying the molecular structure through techniques like metallocene catalysis.
- High Impact Resistance HDPE Pipes and Tubes: Several patents describe the development of HDPE pipes and tubes with improved impact resistance, achieved through the use of specific HDPE compositions, reinforcement with materials like glass fibers, or the incorporation of corrugated or double-wall structures.
- High Temperature and Pressure Resistance HDPE Materials: Some patents focus on enhancing the resistance of HDPE materials to high temperatures and pressures, which can also contribute to improved impact resistance, involving the use of specialized additives, reinforcements, or the development of composite materials.
- Antioxidant and Aging Resistant HDPE Materials: Several patents describe the incorporation of antioxidants or other additives into HDPE materials to improve their resistance to aging, oxidation, and environmental factors, which can also enhance their overall durability and impact resistance.
- Conductive and Antistatic HDPE Materials: Some patents focus on the development of conductive or antistatic HDPE materials, achieved through the incorporation of conductive fillers or the use of specialized polymer blends, which can have improved impact resistance and other desirable properties.
02 HDPE Composites with Improved Impact Resistance
Composite materials based on HDPE have been formulated to achieve enhanced impact resistance, including reinforcements such as glass fibers, carbon fibers, or nanofillers, which improve the impact strength of the material.03 Impact-Resistant HDPE Pipes and Structures
HDPE pipes and structures have been designed with improved impact resistance for various applications, involving specific material compositions, reinforcements, or structural designs to enhance the impact strength of the products.04 HDPE Alloys and Blends for Impact Resistance
HDPE has been alloyed or blended with other polymers or additives to improve its impact resistance, combining the properties of different materials to achieve enhanced impact strength.05 Impact-Resistant HDPE Films and Membranes
HDPE films and membranes have been developed with improved impact resistance for various applications, involving specific material compositions, reinforcements, or processing techniques to enhance the impact strength of the films and membranes.
Key Players in HDPE Industry
The competitive landscape for improving the impact resistance of HDPE is characterized by established industry leaders and emerging players. The industry is mature, driven by applications in packaging, construction, and automotive sectors. Key players like Borealis AG, SABIC Global Technologies BV, Dow Global Technologies LLC, and ExxonMobil Chemical Patents, Inc. showcase advanced R&D capabilities, while emerging companies like Suzhou Sunway Polymer Co., Ltd. and Tianjin Kingfa Advanced Materials Co. Ltd. indicate a dynamic market.
Borealis AG
Technical Solution: Borealis AG's Borstar technology enhances HDPE impact resistance by optimizing polymer structure, enabling improved mechanical properties for demanding applications.
Strength: Advanced polymer structure optimization. Weakness: High production cost.
SABIC Global Technologies BV
Technical Solution: SABIC's new HDPE grade with enhanced impact resistance uses advanced catalyst technology, improving toughness and durability for packaging and construction applications.
Strength: Advanced catalyst technology. Weakness: Limited availability of raw materials.
Core Innovations in HDPE Impact Resistance
Modified high-density polyethylene material and preparation method thereof
PatentActiveCN108384089A
Innovation
- The modifier is an amine-terminated polyol ester compound or a cyclic multipolymer, which can effectively improve the compatibility of active nano-calcium carbonate with high-density polyethylene, improve mechanical properties and molding processing properties
- The pre-treated nano-calcium carbonate is coated with sodium stearate on the surface to improve its compatibility with high-density polyethylene, and after drying, it is easier to disperse in high-density polyethylene
- The high-density polyethylene and active nano-calcium carbonate are mixed and sent to a twin-screw extruder for melt extrusion to achieve uniform mixing of active nano-calcium carbonate and high-density polyethylene, and after water tank cooling, pelletizing and drying, a modified high-density polyethylene material is obtained
- The temperature of each zone of the twin-screw extruder can be adjusted as needed to meet the needs of different applications
- The preparation method of the modified high-density polyethylene material is simple and easy to meet the needs of different applications
Regulatory Standards for HDPE Materials
High-density polyethylene (HDPE) is a widely used thermoplastic polymer known for its excellent chemical resistance, durability, and cost-effectiveness. However, its impact resistance remains a challenge, limiting its applications in areas where high impact strength is required. Improving the impact resistance of HDPE has been a subject of extensive research and development efforts.
The research aims to explore innovative approaches to enhance the impact resistance of HDPE while preserving its desirable properties. This could involve modifying the polymer structure, incorporating reinforcing fillers or additives, or developing novel processing techniques. Potential solutions may include copolymerization, blending with impact modifiers, or employing advanced manufacturing methods like reactive extrusion or nanocomposite formation.
the structure of the environmentally friendly knitted fabric provided by the present invention; figure 2 Flow chart of the yarn wrapping machine for environmentally friendly knitted fabrics and storage devices; image 3 Is the parameter map of the yarn covering machine
Login to View More Environmental Impact of HDPE Innovations
High-density polyethylene (HDPE) is a widely used thermoplastic polymer known for its excellent chemical resistance, durability, and cost-effectiveness. However, its impact resistance remains a challenge, limiting its applications in areas where impact loads are prevalent. Improving the impact resistance of HDPE is crucial for expanding its usage in various industries.
The research on enhancing HDPE's impact resistance has focused on modifying its molecular structure and incorporating reinforcing fillers or additives. Strategies like copolymerization, blending with elastomers, and incorporating nanofillers have shown promising results. Additionally, advanced processing techniques, such as reactive extrusion and solid-state shear pulverization, have been explored to improve the material's toughness.
Ongoing research efforts aim to develop cost-effective and scalable solutions that can be integrated into existing manufacturing processes. Potential innovations may involve novel polymer architectures, synergistic filler combinations, or innovative processing methods that can impart superior impact resistance while maintaining HDPE's desirable properties.
the structure of the environmentally friendly knitted fabric provided by the present invention; figure 2 Flow chart of the yarn wrapping machine for environmentally friendly knitted fabrics and storage devices; image 3 Is the parameter map of the yarn covering machine
Login to View More If you want an in-depth research or a technical report, you can always get what you want in Patsnap Eureka TechResearch . Try now!