Research on improving the heat resistance of HDPE (High-Density Polyethylene) - Eureka
OCT 8, 20244 MIN READ
Generate Your Technical Report in Patsnap Eureka
AI-Powered Innovation Solution Platform for R&D
HDPE Heat Resistance Challenges and Goals
The primary objective is to investigate and develop solutions for enhancing the heat resistance of high-density polyethylene (HDPE), a widely used thermoplastic polymer. HDPE is known for its excellent chemical resistance, durability, and cost-effectiveness, but its relatively low heat resistance limits its applications in certain industries.
Improving the heat resistance of HDPE would expand its potential applications in areas such as automotive, electrical, and construction, where exposure to high temperatures is common. This could lead to the development of more durable and reliable products, ultimately benefiting various sectors and contributing to technological advancements.
Improving the heat resistance of HDPE would expand its potential applications in areas such as automotive, electrical, and construction, where exposure to high temperatures is common. This could lead to the development of more durable and reliable products, ultimately benefiting various sectors and contributing to technological advancements.
Market Demand for Heat-Resistant HDPE
- Growing Demand
The demand for heat-resistant HDPE is steadily increasing due to its wide range of applications in industries such as automotive, construction, and packaging, where high-temperature resistance is crucial. - Expanding Applications
As new technologies emerge, the need for heat-resistant HDPE is expanding into areas like renewable energy, aerospace, and electronics, driving further market growth. - Regulatory Compliance
Stringent regulations and safety standards in various industries are driving the adoption of heat-resistant HDPE to meet compliance requirements for high-temperature applications. - Replacement of Traditional Materials
Heat-resistant HDPE is increasingly replacing traditional materials like metals and ceramics in certain applications due to its superior properties, such as lightweight, corrosion resistance, and cost-effectiveness. - Emerging Economies
Rapid industrialization and infrastructure development in emerging economies are fueling the demand for heat-resistant HDPE in sectors like construction, transportation, and manufacturing.
Current State and Limitations of HDPE Heat Resistance
- Limited Heat Resistance
HDPE exhibits relatively low heat resistance compared to other engineering plastics, with a maximum continuous use temperature around 120°C. - Thermal Degradation
Prolonged exposure to high temperatures can lead to oxidative degradation, chain scission, and cross-linking, compromising HDPE's mechanical and physical properties. - Processing Challenges
The high melt viscosity and narrow processing window of HDPE pose challenges in manufacturing processes involving high temperatures, such as extrusion and injection molding. - Geographical Limitations
HDPE's heat resistance limitations restrict its applications in regions with extreme climates or industries requiring high-temperature operations.
Evolution of HDPE Heat Resistance Technologies
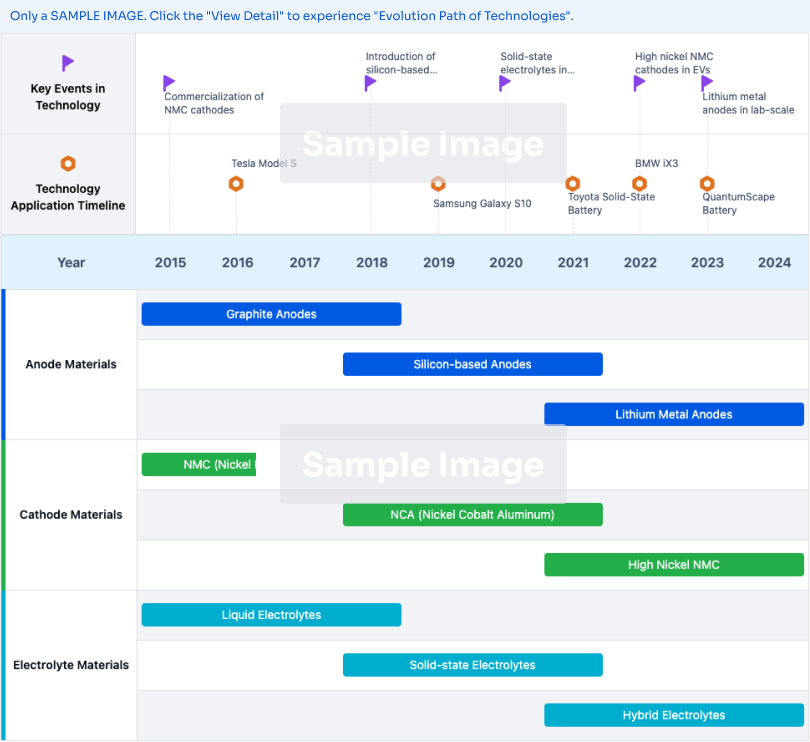
Existing Solutions for Enhancing HDPE Heat Resistance
01 High-temperature resistance of HDPE materials
Use of additives, fillers, or blending with other polymers to improve thermal stability and heat resistance of HDPE products.- High-temperature resistance of HDPE materials: Techniques to enhance thermal stability and heat resistance of HDPE, including additives, fillers, or reinforcements, for applications requiring exposure to elevated temperatures.
- Aging and weathering resistance of HDPE: Incorporation of antioxidants, UV stabilizers, or other additives to protect HDPE from degradation caused by environmental factors, extending service life.
- Reinforced and composite HDPE materials: Fiber-reinforced HDPE composites, HDPE blends with other polymers, and HDPE composites with inorganic fillers or reinforcements for improved mechanical strength, impact resistance, or other properties.
- Conductive and antistatic HDPE materials: Incorporation of conductive fillers or additives into HDPE matrix for dissipating static electricity and providing electrostatic discharge (ESD) protection.
- Recycling and reuse of HDPE materials: Techniques for recovering and processing post-consumer or post-industrial HDPE waste into new products or materials, potentially with virgin HDPE or additives to enhance properties.
02 Aging and weathering resistance of HDPE
Modification with antioxidants, UV stabilizers, or other additives to prevent degradation and maintain properties under harsh environmental conditions.03 Reinforced and composite HDPE materials
Incorporation of reinforcing fibers, fillers, or blending with other polymers to create composite or reinforced HDPE materials with improved strength, impact resistance, and other properties.04 Antistatic and conductive HDPE materials
Modification with conductive fillers or additives to enable the development of antistatic or conductive HDPE products for specific applications.05 Recycling and reuse of HDPE materials
Techniques for recycling and reusing HDPE materials, often involving the recovery and reprocessing of post-consumer or post-industrial HDPE waste, promoting sustainability.
Key Players in HDPE Industry
The competitive landscape for improving the heat resistance of HDPE is characterized by established industry leaders and research institutions. The industry is mature with significant market size, driven by demand in automotive, construction, and packaging sectors. Key players like SABIC, ExxonMobil, and Dow have advanced research capabilities and extensive patent portfolios, indicating high technical maturity. Emerging contributions from academic institutions suggest potential for future breakthroughs.
SABIC Global Technologies BV
Technical Solution: SABIC has developed a proprietary technology for enhancing the heat resistance of HDPE by incorporating advanced stabilizers and cross-linking agents, improving thermal stability and mechanical properties.
Strength: High thermal stability. Weakness: Potential increase in production costs.
China Petroleum & Chemical Corp.
Technical Solution: China Petroleum & Chemical Corp. focuses on using nanocomposites to enhance the heat resistance of HDPE, integrating nano-sized fillers to improve thermal and mechanical properties.
Strength: Enhanced mechanical properties. Weakness: Complexity in manufacturing process.
Core Innovations in HDPE Heat Resistance
Modified high-density polyethylene material and preparation method thereof
PatentActiveCN108384089A
Innovation
- 改性剂选用端胺基多元醇酯化合物或一种环链式多元聚合物,可有效提高活性纳米碳酸钙与高密度聚乙烯的相容性,改善力学性能和成型加工性能
- 预处理纳米碳酸钙经硬脂酸钠表面包覆处理,可提高与高密度聚乙烯的相容性,并经干燥处理,使之更易分散在高密度聚乙烯中
- 将高密度聚乙烯和活性纳米碳酸钙混合,送入到双螺杆挤出机中熔融挤出,可实现活性纳米碳酸钙与高密度聚乙烯的均匀混合,并经水槽冷却、切粒和干燥处理,得到改性高密度聚乙烯材料
- 双螺杆挤出机各区的温度可根据需要进行调节,以适应不同应用的需要
- 改性高密度聚乙烯材料的制备方法简单易行,可满足不同应用的需要
Environmental Impact of Heat-Resistant HDPE
High-density polyethylene (HDPE) is a widely used thermoplastic polymer with excellent chemical resistance, impact strength, and cost-effectiveness. However, its heat resistance is relatively low, limiting its applications in high-temperature environments. Improving the heat resistance of HDPE has become a crucial research area to expand its potential applications.
The research aims to develop innovative solutions that can enhance the thermal stability and heat resistance of HDPE without compromising its desirable properties. This could involve exploring various approaches, such as incorporating heat-resistant additives, modifying the polymer structure through chemical or physical means, or developing composite materials with improved thermal properties.
Potential solutions may include the use of nanofillers, like carbon nanotubes or graphene, to create HDPE nanocomposites with enhanced thermal conductivity and heat dissipation capabilities. Additionally, chemical modifications, such as crosslinking or grafting heat-resistant functional groups onto the HDPE backbone, could improve its thermal stability. Exploring the synergistic effects of combining multiple strategies may also yield promising results.
the structure of the environmentally friendly knitted fabric provided by the present invention; figure 2 Flow chart of the yarn wrapping machine for environmentally friendly knitted fabrics and storage devices; image 3 Is the parameter map of the yarn covering machine
Login to View More Regulatory Landscape for HDPE Products
High-density polyethylene (HDPE) is a widely used thermoplastic polymer with excellent chemical resistance, mechanical strength, and durability. However, its heat resistance is relatively low, limiting its applications in high-temperature environments. Improving the heat resistance of HDPE is crucial for expanding its potential applications.
The research aims to explore innovative approaches to enhance the thermal stability and heat resistance of HDPE. This could involve modifying the polymer structure, incorporating additives or fillers, or developing new processing techniques. Potential solutions may include crosslinking, blending with heat-resistant polymers, or incorporating nanofillers like carbon nanotubes or graphene. The research should evaluate the effectiveness, feasibility, and scalability of these approaches while considering cost, environmental impact, and compatibility with existing manufacturing processes.
the structure of the environmentally friendly knitted fabric provided by the present invention; figure 2 Flow chart of the yarn wrapping machine for environmentally friendly knitted fabrics and storage devices; image 3 Is the parameter map of the yarn covering machine
Login to View More If you want an in-depth research or a technical report, you can always get what you want in Patsnap Eureka TechResearch . Try now!