Research on improving the dispersion properties of HDPE - Eureka
OCT 8, 20244 MIN READ
Generate Your Technical Report in Patsnap Eureka
AI-Powered Innovation Solution Platform for R&D
HDPE Dispersion Challenges and Goals
The primary objective is to investigate and improve the dispersion properties of high-density polyethylene (HDPE), a widely used thermoplastic polymer. Achieving good dispersion is crucial for enhancing the material's processability, mechanical properties, and overall performance.
Key challenges include overcoming the inherent hydrophobic nature of HDPE, which can lead to agglomeration and poor dispersion of additives or fillers. Additionally, optimizing processing conditions, such as shear forces and temperature, plays a vital role in achieving uniform dispersion and preventing phase separation or degradation.
Key challenges include overcoming the inherent hydrophobic nature of HDPE, which can lead to agglomeration and poor dispersion of additives or fillers. Additionally, optimizing processing conditions, such as shear forces and temperature, plays a vital role in achieving uniform dispersion and preventing phase separation or degradation.
Market Demand for Enhanced HDPE Dispersion
- Growing Demand for Enhanced Dispersion
The market demand for high-density polyethylene (HDPE) with improved dispersion properties is driven by various industries, including:
- Packaging: Better dispersion enhances the uniformity and barrier properties of HDPE films and containers.
- Automotive: Improved dispersion leads to better mechanical properties and surface finish in HDPE components.
- Construction: Enhanced dispersion improves the durability and weathering resistance of HDPE pipes and geomembranes.
- Market Potential and Trends
- The global HDPE market is projected to grow steadily, driven by increasing demand from the packaging, automotive, and construction sectors.
- There is a growing trend towards using HDPE with enhanced properties, including improved dispersion, to meet stricter performance requirements.
- Emerging markets in Asia-Pacific and the Middle East are expected to contribute significantly to the demand for enhanced HDPE products.
- Competitive Landscape
- Major HDPE producers, such as ExxonMobil, LyondellBasell, and Dow Chemical, are investing in research and development to improve the dispersion properties of their HDPE products.
- Specialty chemical companies, like Milliken & Company and Clariant, offer additive solutions to enhance the dispersion of HDPE.
- Collaboration between HDPE producers and additive manufacturers is expected to drive innovation in this area.
Current State and Limitations of HDPE Dispersion
- Limited Dispersion Capability
HDPE exhibits poor dispersion properties due to its non-polar nature and high molecular weight, making it challenging to achieve uniform dispersion in various media. - Agglomeration and Settling
HDPE particles tend to agglomerate and settle rapidly, leading to non-uniform distribution and potential performance issues in applications requiring stable dispersions. - Surface Modification Challenges
Modifying the surface properties of HDPE to improve dispersion is difficult due to its inert chemical nature and resistance to chemical reactions. - Compatibility Issues
HDPE often exhibits poor compatibility with polar solvents, surfactants, and other additives commonly used to enhance dispersion stability. - Processing Limitations
Conventional dispersion techniques, such as high-shear mixing or ultrasonication, may not be effective for HDPE due to its high molecular weight and tendency to degrade under intense shear forces.
Evolution of HDPE Dispersion Technologies
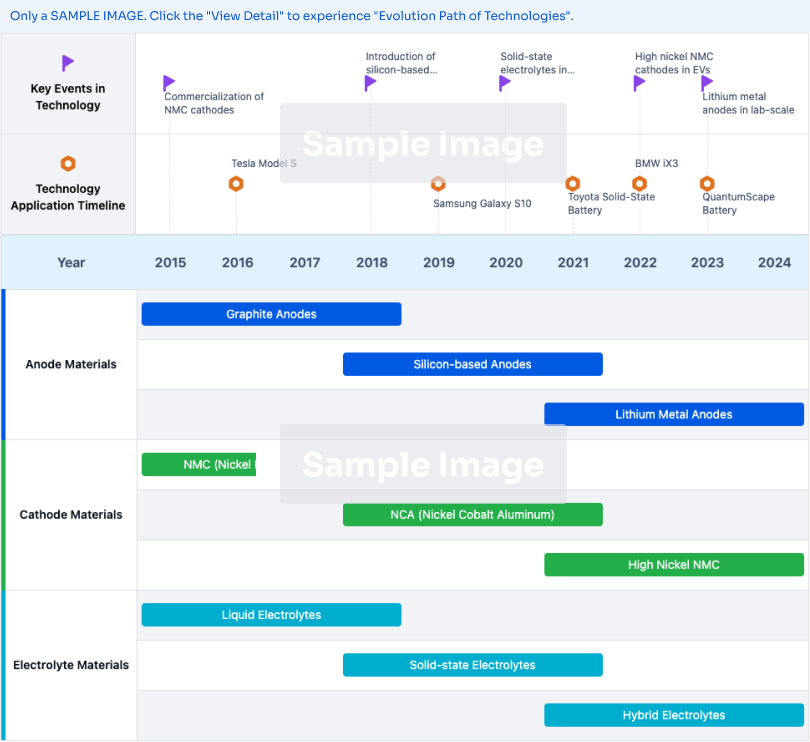
Existing Solutions for HDPE Dispersion Improvement
01 HDPE Composite Materials
Various composite materials are developed by incorporating different fillers or additives into HDPE to enhance properties like reinforcement, conductivity, heat transfer, and flame retardancy for applications in construction, transportation, and electrical insulation.- HDPE Composite Materials: Various composite materials are developed by combining HDPE with other materials such as minerals, fibers, or polymers to enhance properties like strength, conductivity, heat transfer, and foaming. These composites find applications in areas like construction, packaging, and insulation.
- HDPE Alloys and Blends: HDPE is alloyed or blended with other polymers like LDPE, PP, or metallocene polyethylene to improve properties like pressure resistance, fire retardancy, and antistatic behavior. These alloys and blends are used in applications such as pipes, films, and packaging materials.
- HDPE Pipe and Film Materials: HDPE is widely used in the production of pipes and films due to its durability and chemical resistance. Various formulations and processing methods are developed to enhance properties like strength, aging resistance, and high-temperature resistance for specific applications.
- HDPE Foaming and Extrusion Processes: Techniques like foaming and extrusion are employed to produce HDPE products with specific properties like low density, high magnification, or continuous profiles. These processes are used to manufacture materials like foam cores, sheets, and extruded profiles.
- HDPE Modification and Recycling: Methods are developed to modify HDPE properties through techniques like chemical treatment, reinforcement, or the addition of additives. Additionally, processes for recycling and reusing HDPE materials are explored to promote sustainability.
02 HDPE Alloys and Blends
HDPE is alloyed or blended with other polymers like LDPE, PP, or metallocene polyethylene to improve properties or create new materials with desired characteristics like enhanced pressure resistance, fire retardancy, or antistatic properties.03 HDPE Pipe and Film Materials
HDPE is widely used in the production of pipes and films due to its excellent chemical resistance, durability, and processability. Various techniques are employed to improve properties like reinforcement, aging resistance, and high-temperature resistance for specific application requirements.04 HDPE Foaming and Extrusion Processes
HDPE can be foamed or extruded to produce lightweight, insulating materials or products with specific shapes and structures. These processes involve techniques like high-magnification foaming, coextrusion, and continuous extrusion to achieve desired properties and applications.05 HDPE Recycling and Modification
Efforts are made to recycle and modify HDPE materials to reduce waste and improve properties. This includes processes like reclaiming HDPE materials, modifying HDPE pipelines, and incorporating antioxidants or other additives to enhance performance and durability.
Key Players in HDPE Industry
The competitive landscape for improving the dispersion properties of HDPE is characterized by established industry leaders and emerging players. The industry is mature, driven by the demand for high-performance materials. Key players like Dow Global Technologies LLC, ExxonMobil Chemical Patents, Inc., and SABIC Global Technologies BV have advanced R&D capabilities, contributing to high technical maturity. Companies like China Petroleum & Chemical Corp. and Borealis AG are also making significant strides, indicating a competitive and innovation-driven market.
Dow Global Technologies LLC
Technical Solution: Dow Global Technologies LLC has developed advanced catalysts and process technologies to improve the dispersion properties of HDPE, enhancing the polymer matrix and optimizing the distribution of fillers and additives.
Strength: Advanced catalyst technology. Weakness: High cost of implementation.
ExxonMobil Chemical Patents, Inc.
Technical Solution: ExxonMobil Chemical Patents, Inc. offers a proprietary technology using specific co-monomers and advanced polymerization techniques to enhance the dispersion properties of HDPE, achieving uniform particle distribution and improved mechanical properties.
Strength: Proven industrial application. Weakness: Limited flexibility in polymer customization.
Core Innovations in HDPE Dispersion
Modified high-density polyethylene material and preparation method thereof
PatentActiveCN108384089A
Innovation
- The modifier is an amine-terminated polyol ester compound or a cyclic multipolymer, which can effectively improve the compatibility of active nano-calcium carbonate with high-density polyethylene, improve mechanical properties and molding processing properties
- The pre-treated nano-calcium carbonate is coated with sodium stearate on the surface to improve its compatibility with high-density polyethylene, and after drying, it is easier to disperse in high-density polyethylene
- The high-density polyethylene and active nano-calcium carbonate are mixed and sent to a twin-screw extruder for melt extrusion to achieve uniform mixing of active nano-calcium carbonate and high-density polyethylene, and after water tank cooling, pelletizing and drying, a modified high-density polyethylene material is obtained
- The temperature of each zone of the twin-screw extruder can be adjusted as needed to meet the needs of different applications
- The preparation method of the modified high-density polyethylene material is simple and easy to meet the needs of different applications
Environmental Impact of HDPE Dispersion
High-density polyethylene (HDPE) is a widely used thermoplastic polymer with excellent mechanical properties, chemical resistance, and cost-effectiveness. However, its poor dispersion properties can limit its applications in certain fields. Improving the dispersion properties of HDPE is crucial for enhancing its performance and expanding its potential uses. This research aims to explore innovative approaches to modify HDPE's molecular structure and composition, enabling better dispersion in various media. Potential solutions may involve incorporating functional groups, blending with compatible additives, or employing advanced processing techniques. The ultimate goal is to develop HDPE materials with superior dispersion capabilities while maintaining their desirable characteristics, opening up new opportunities in industries such as coatings, composites, and advanced materials.
the structure of the environmentally friendly knitted fabric provided by the present invention; figure 2 Flow chart of the yarn wrapping machine for environmentally friendly knitted fabrics and storage devices; image 3 Is the parameter map of the yarn covering machine
Login to View More Regulatory Landscape for HDPE Products
High-density polyethylene (HDPE) is a widely used thermoplastic polymer with excellent mechanical properties, chemical resistance, and cost-effectiveness. However, its poor dispersion properties can limit its applications in certain fields. Improving the dispersion properties of HDPE is crucial for enhancing its performance and expanding its potential applications.
The dispersion properties of HDPE are influenced by factors such as molecular weight, molecular weight distribution, and the presence of additives or fillers. Strategies to improve dispersion may involve modifying the polymer structure, incorporating compatibilizers, or employing advanced processing techniques. Potential approaches include copolymerization, grafting, reactive extrusion, and the use of nanofillers or surface modifiers.
Enhancing the dispersion properties of HDPE can lead to improved processability, better filler distribution, and enhanced mechanical, thermal, and electrical properties in various applications, such as packaging, automotive, construction, and electronics industries. Ongoing research efforts aim to develop cost-effective and scalable solutions while maintaining the desirable properties of HDPE.
the structure of the environmentally friendly knitted fabric provided by the present invention; figure 2 Flow chart of the yarn wrapping machine for environmentally friendly knitted fabrics and storage devices; image 3 Is the parameter map of the yarn covering machine
Login to View More If you want an in-depth research or a technical report, you can always get what you want in Patsnap Eureka TechResearch . Try now!